Channels lising page
All videos archived of Hyperspace Pirate

_nKihWAYrEM | 14 Jul 2025
Go to https://ground.news/hyperspacepirate for a better way to stay informed. Subscribe for 40% off unlimited access to world-wide coverage through my link. In this video I'll show the process of building my 1,500 watt HHO gas generator. The generator is comprised of three "modules" consisting of 21 plates (20 cells) of 2" x 6" 316 stainless steel spaced 4mm apart in a solution of 20 percent NaOH (Sodium Hydroxide). The cells are placed in a 3d-printed ABS casing to prevent leakage current from bypassing the plates through surrounding electrolyte. The electrolysis cells are sealed inside of re-purposed water filter casings that can hold large amount of pressure. Each module is powered by its own a 48-volt 12.5 amp power supply. At 48V, the modules pull 10 amps, and the system as a whole produces around 5 L/min of HHO gas. The gas is passed through a bubbler, which doesn't really clean contaminants out of the gas stream, but prevents flashback into the electrolysis cells of the modules. A mist of fine particles of sodium hydroxide exits the system with the gas, producing a bright orange flame, which would otherwise be almost invisible due to burning only hydrogen. At 2,800C, the flame is hot enough to melt steel, rocks, glass, sand, and so forth. Without excess fuel in the gas stream, the hydrogen flame is unable to weld steel because the superheated water vapor exhaust simply oxidizes the iron to black iron oxide (magnetite). However, the oxidizing flame makes the torch relatively effective at cutting steel up to 3-4mm. Naturally, I also played with exploding balloons a little bit too. Igniting HHO creates a detonation with a velocity of around 3,000 m/s, but the peak pressure is only around 20-atmospheres, meaning it's not powerful enough to do any real damage to solid material if it's unconfined. The main hazard is hearing damage, although I'd still recommend wearing eye protection when handling anything with HHO. With propane injected into the HHO stream, I think the flame could be made fuel-rich enough to weld steel (though at the expense of maximum temperature). I think the main use of this type of device is in welding/melting/cutting borosilicate glass, which could be extremely useful for people who need special custom glassware setups for chemistry. There's also the potential of integrating the head into a CNC sheet metal cutter. Music Used: Kevin MacLeod - George Street Shuffle Kevin MacLeod - Apero Hour Kevin MacLeod - Groove Groove

CLX_pQbSFFg | 07 Jun 2025
Click this link https://sponsr.is/bootdev_HyperspacePirate and use my code HYPERSPACEPIRATE to get 25% off your first payment for boot.dev. In this video I'll show how I built a hand-cranked generator capable of producing up to 3,000 volts AC from the output, and over 20,000 volts DC when it's attached to a voltage multiplier. Then, using a vacuum chamber, I'll generate plasma discharges with the high voltage, so it'll all be done by hand. The generator consists of a hand crank with a 4.5:1 overdrive gear connected to a rotor with 4 40x20 N52 cylindrical magnets. The stator consists of 8 coils in series, each with 14,700 turns of 38-gauge wire, for a total winding resistance of 25.6 kOhm. There's also a separate small coil and magnet on the rotor shaft for getting a low-voltage RPM signal that my oscilloscope can read. The coils were slowly and carefully wound with a 100-rpm gear motor running lower than the rated voltage to minimize pull force on the ultra-fine magnet wire. Each coil took approximately one hour to wind. The average resistance of each coil is approximately 3.2 kOhm and in total there's 11.4 km or 7.2 miles of wire on the stator coils. The peak voltage is ~3kV at just a little over 1,200 RPM on the rotor (unloaded). Maximum short circuit current measured by hand cranking was ~35 mA. The maximum power delivered to a load was 16W, although when adding that to the i^2R losses through the stator coils, the total power into the generator was 28W, making the whole thing a little over 50% efficient at maximum power. At lower power, the efficiency is closer to 80-90%. The main drawback of this design is that the stator coils don't use ferrous cores. This is because the rotor magnets are so strong that they would rip the ferrous cores out of their sockets and make the generator extremely difficult to turn at low RPM due to cogging. The upside to this is that the generator has practically zero startup torque, and without a load, the flywheel momentum of the rotor can keep it spinning for a relatively long time. Plasma could also be manually generated with a device called a wimshurst machine, which is an electrostatic generator, whereas mine is electromagnetic. The advantage of mine is that it can deliver more power than a wimshurst machine, and the 8 coils could also be reconfigured to different series/parallel combinations for different peak voltage/current. It also outputs alternating current, which allows it to be used in more types of circuits, whereas the winshurst machine is purely DC.

HZYWpZYuRKc | 12 May 2025
Take back your personal data with Incogni! Use code "hpirate" at the link below and get 60% off an annual plan: https://incogni.com/hpirate In this video I'll be demonstrating how nitrates can be made from the ozone generated from high voltage discharges. This is different from the "Birkeland-Eyde" process, which uses a white-hot high voltage arc to create NO2 to synthesize Nitric Acid. With the ozone method, O3 is generated from either Corona discharge or Dielectric Barrier discharge, which is similar to corona but acts over a large area. Unlike arcs or sparks, these types of discharges are non-thermal plasmas, and theoretically they don't produce any oxides of nitrogen. Rather, they create ozone from atmospheric oxygen by the following reaction: 2O2 → 2O3 The Ozone (O3) is an extremely powerful and unstable oxidizer than can be used to synthesize a number of different compounds. When added to Ammonia (NH3), it forms ammonium nitrate by the following reaction: 2NH3 + 4O3 → NH4NO3 + 4O2 +H2O The ammonium nitrate can then be used as a fertilizer, converted into nitrous oxide, used to make nitric acid, or used as part of a mixture for a blasting agent. I ran experiments with both large-gap / small area corona discharges at 150,000 volts, and small-gap / large area dielectric barrier discharges at a few volts. The dielectric barrier discharges produced more ozone per unit energy by far, which i determined by the use of an ozone meter. Unfortunately, when bubbling the ozone through a solution of ammonia, the maximum yield per unit energy was 0.33 grams of ammonium nitrate per kWh. In contrast, the maximum yield I achieved with a Birkeland-Eyde reactor was around 12.7g/kWh - nearly two orders of magnitude greater. The production of ozone still has lots of other uses that I intend to investigate in the future, such as the production of sulfuric acid directly from sulfur. It's also extremely effective and sterilizing large areas and removing bad smells due to it's ability to attack microbes and insects. This is similar to fumigating, but without the hassle of closing off an entire house. Ozone rapidly decays back into O2, so even if hazardous concentrations are present in a living space, they're typically safe after a few hours. In a future video I'll experiment with a higher power ozone generator fed by nearly 100% oxygen.

4NRkFqeO27Y | 08 Apr 2025
Click this link https://sponsr.is/bootdev_HyperspacePirate and use my code HYPERSPACEPIRATE to get 25% off your first payment for boot.dev. In this video I'll show how I built my own portable X-ray machine used for imaging electronics and other small objects. I initially used a KL-0.8-70 tube, but ended up using a KL11-0.4-70 tube for the final iteration. The anode is supplied high voltage by a 10-stage voltage multiplier using pairs of 1nF / 20kV capacitors in series and 100mA / 20kV diodes in series. Unloaded, it can output close to 120kV DC, but with the tube running, it puts out 50-70kV depending on the cathode current. The voltage multiplier is fed by a high voltage transformer driven by a ZVS driver at 24V DC. The transformer is made of 2 flyback transformer cores and has 4 turns on the primary and 750 turns on the secondary. It's voltage output is around 12kV peak unloaded. The transformer is submerged in mineral oil and was out-gassed under vacuum. The cathode heater current is supplied by an adjustable DC-DC buck converter I built. To get a good picture on the KL11-0.4-70 tube, I set the cathode current between 2.1-2.4 amps, but I found 2.3 amps to give the brightest and clearest picture. This number is highly dependent on the power of the anode power supply, and a more powerful supply would be able to provide a picture at a higher cathode current without pulling down the voltage excessively. The X-ray tube is housed inside an enclosure filled with mineral oil, which keeps it cooled, but also helps insulate the high voltage anode and block the bright light from the cathode heater (because the inside of the screen chamber needs to be as dark as possible). I also added a remote control, which allows the operator to stand far away from the machine for improved safety, and a timer circuit that limits the maximum on-time of the x-ray tube to 0.92 seconds, to prevent excessive radiation or overheating. The radiation levels immediately outside the machine were measured at ~0.5-1.0 uSv/h over a 1-minute average with a single 0.92 second shot being taken during that period. These levels fall off rapidly with distance, and at 10-15m away, a dosimeter barely registers a difference relative to background radiation. Schematic: https://drive.google.com/file/d/1Pz6mCtcKRF6M_m9eBsqdajyPbvOGoDZC/view?usp=sharing Music Used: Kevin MacLeod - Groove Groove

adTKHcrOzMU | 14 Mar 2025
In this video I'll be attempting to get the longest range possible out of a wireless power transmission system using inductive coupling. I'll start off with a "blocking" oscillator (similar to a joule theif) running off a 9-volt battery, and work my way up to a resonant half-bridge driver powered from 120 volts AC. The maximum range I achieved for lighting a single LED was 130 ft (40m), and the open circuit voltage at that range was about 2.6V. The wireless power transmitter is a 15-ft (4.6m) hexagon with 8 turns of 14-gauge wire that oscillates at approximately 145 kHz. This frequency is used because it's the resonant frequency of the coil when paired with a 1.32 nF capacitor. With a 120-volt DC input, the peak voltage across the coil can excess 10,000 volts. The reason this is possible without a transformer is because the high voltage peaks are on the opposite side of the coil from the MOSFET drivers, which only see voltage between VCC and GND. The catch is that the resonant capacitor has to be rated for the huge voltage produced (and also handle large currents), but this is relatively easy to do by using lots of small low-ESR film capacitors in series/parallel combinations. My capacitor bank used 100 33nF capacitors rated at 630VAC (2 parallel sets of 50 in series). This sort of capacitor bank looks and functions pretty much exactly the same as the "MMC" banks used on spark-gap tesla coils, and dual-resonant solid state tesla coils. By tuning the reciever coil to resonate at the same frequency as the transmitter, maximum power transfer can be achieved. I also added a diode and capacitor in parallel with the reciever's resonant caps to serve as a "peak detector" so that I could conveniently read peak voltage at resonance with a cheap handheld multimeter. The reciever I used in this video has an output impedance of about 11 kOhms, so while it's not a very good current source, it was capable of generating tremendous voltages when it was open- circuit. The major weakness of inductive coupling with air-cored coils is that the power transfer is heavily dependant on the geometry of the transmitter and reciever coils, and the power that can be recieved at a given distance falls off dramatically with reciever diameter. From an RF standpoint, these coils are basically electrically short antennas, so better coupling could probably be achieved at much higher frequencies where the coils are sized at one-quarter or one-half the wavelength of the transmission frequency. Music Used: Kevin MacLeod - Backbay Lounge

agwKNLoU6g8 | 20 Jan 2025
Click this link https://sponsr.is/bootdev_HyperspacePirate and use my code HYPERSPACEPIRATE to get 25% off your first payment for boot.dev. In this video I'll demonstrate the incredible power of electricity when it's stored at high voltage in a large capacitor bank. This device uses five 10,000 uF 400-volt capacitors in series, forming a bank with 2,000 uF and a maximum voltage of 2,000 volts. At full charge, it stores 4kJ of energy, which is approximately equivalent to the chemical energy in one gram of TNT. When the switch is closed, the capacitors dump more than 10,000 amps of current through an extremely thin wire, causing it to heat so rapidly that it explodes with tremendous pressure, causing a bright flash, a shockwave, and tremendous noise. This type of electrical explosion can be used in lieu of a chemical blasting cap, and in fact, was used to detonate the compression charges in plutonium-based nuclear weapons. Unlike a chemical blasting cap, an exploding wire can have its timing controlled down to the nanosecond-level, making it suitable for nuclear devices. Exploding wires are also used for plasma research, since the circuit can be configured to create a "Z-pinch" or "X-pinch" effect that generates large X-ray bursts and other interesting high-energy phenomena. For a given energy, an exploding wire circuit should have the largest voltage practical with the lowest capacitance possible to minimize RC time constant and discharge time, and maximize current rise time and peak current. This means, ideally, the capacitor bank should use high voltage film or oil capacitors. In reality, cost and logistics made electrolytic capacitors the most practical for this project. These have the best energy density, but suffer from relatively large series resistance and inductance. The circuit shown in this video is initially triggered using an Thyristor (SCR), but the extremely high peak current and short rise time caused the device to be destroyed, so I revered to a mechanical switch, which actually worked pretty well. I tried exploding Copper, Aluminum, Nichrome, and Magnesium. Aluminum and Magnesium had the most dramatic effect, because both ignited when superheated by the electric current, causing them to add their chemical energy to the blast. I've tried up to 500 milligrams of aluminum foil, and in every test, the aluminum is totally vaporized from ignition. I'm not really sure if there's a practical application that I can use this device for, but it's extremely fun to use, and if you don't have any fireworks for special occasions, it certainly provides a good substitute. Music Used: Kevin MacLeod - Lobby Time Kevin MacLeod - Groove Groove

AZqjMaiJZMQ | 13 Dec 2024
Head to https://squarespace.com/hyperspacepirate to save 10% off your first purchase of a website or domain using code HYPERSPACEPIRATE Yep - it's another refrigeration video. This time, instead of trying to go as cold as possible, I'm trying to go as big as possible, and I'll be building a 1,600-watt refrigeration system to freeze 25-gallon blocks of ice weighing over 200 lb. Like other refrigeration systems I've built, this system uses rotary compressors and R290 (ordinary propane) as a refrigerant. But this particular system has a twist: it uses two compressors with different power levels running in parallel. As weird as that may sound, it works perfectly. The first compressor was made for R410A, so it was underloaded when it was used with propane, but instead of replacing it, I simply plumbed a second compressor made for R22 into the same refrigeration circuit. Both compressors have their own condenser coils / fans, but the condenser outputs converge on the expansion valve (which is actually a needle valve for manual tuning). The evaporator consists of nearly 100 ft of 1/2" copper tubing, providing over a square meter of surface area for cooling. The 25-gallon pot sits inside the evaporator coil in a tub filled with a 30% calcium chloride solution to maximize heat transfer to the ice without freezing. The solution does still freeze between -10C to -15C but it makes soft, crumbly ice that's easy to remove the 25-gallon pot from. To remove the giant ice block from the cooling bath, a crane with a winch is used to hoist it up, move it clear of the bath, and lower it onto the garage floor. The pot is then flipped upside down, and as the outer surface warms, the ice inside slides clear of the pot. The Ice is then moved either by pushing or wheeling it on a dolly. The ice blocks are then subjected to various experiments for the sake of YouTube entertainment. I'm really not sure if this project has any practical use (aside from maybe a thermal battery?), but the giant ice blocks are a ton of fun to play with, especially in Florida where there's almost never naturally-occuring snow or ice. Music Used: Kevin MacLeod - Local Forecast - Elevator Kevin MacLeod - Bossa Antigua

AiHksObCLuU | 14 Nov 2024
Head to https://squarespace.com/hyperspacepirate to save 10% off your first purchase of a website or domain using code HYPERSPACEPIRATE In this video I'll show how to make Acetylene gas (C2H2) from Seashells and Driftwood. Acetylene gas is formed when Calcium Carbide (CaC2) comes into contact with water. Calcium Carbide can be made by reacting Calcium Oxide (CaO) with Carbon at temperatures in excess of 2,000C. The Calcium Oxide is produced by thermal decomposition of Calcium Carbonate (CaCO3), aka. Limestone. Seashells are mostly made of Calcium Carbonate, so they're baked in a propane furnace to produce the Calcium Oxide. The Carbon in the reaction comes from Charcoal, which is made by thermal decomposition of the driftwood. When wood is heated in the absence of oxygen, it releases a whole soup of volatile compounds including Methane, Carbon Monoxide, Carbon Dioxide, various other hydrocarbons, Methanol Vapor, Water Vapor, and also some tar and other goo. What's left behind is Charcoal, which is almost entirely Carbon, but with trace amounts of Potassium, Sodium, Sulfur, Phosphorous and a few other compounds. Once the Calcium Oxide and Carbon are produced, they're ground up together in a blender to make sure they're mixed as well as possible and have extremely small particle sizes to make the reaction progress easier. The temperature required for the reaction is too hot for an air breathing flame, and I don't have an oxy-fuel system, so I used an Electric Arc Furnace to heat the powder mixture. The arc was supplied with 31VAC from a winding added to the transformer of a 110/220V converter box, which can handle up to 3 kW. Later, I had to reduced the voltage to 15VAC after melting off the windings. There's no obvious visual indicator that Calcium Carbide has been formed, but due to the impurities in the reagents, it has a very prominent garlic-like smell that makes its presence obvious. Once the Carbide is formed, it can be added to water, and Acetylene gas will bubble out. The gas can be collected in a balloon or dissolved in Acetone, but it's unsafe to store it under pressure because it becomes unstable over 3-4 atm. If you have access to elemental Calcium, it's much easier to make the Calcium Carbide, because it only requires mixing with charcoal powder and heating in a test tube with a propane torch.

54Htg4I_ZBA | 26 Oct 2024
Head to https://squarespace.com/hyperspacepirate to save 10% off your first purchase of a website or domain using code HYPERSPACEPIRATE In this video I'll show how I improved my gyro stabilization system by switching from control-moment gyroscopes to a single passive gyroscope on a gimbal with weight shifting to develop stabilizing torque. At rest, the gyroscope is laying flat, but the gimbal is free to rotate about the vehicle's pitch axis. This causes a torque that resists any changes in angle on the vehicle's roll axis, but by itself, isn't able to keep the vehicle upright indefinitely, but rather it serves as an extremely strong roll "damper". By dramatically reducing the roll acceleration produced by a disturbing torque, the stabilizing gyroscope provides a large window of time for correcting the roll, meaning it can actually be stabilized with manual weight shifting - which i demonstrated in the first part of the video by rigging a large ballast weight on a lever to a remote controlled servo. For automated stabilization, the system uses an MPU6050 gyro/accelerometer to provide tilt angle data to an arduino nano, which applies a correction with a weight-shifting servo proportional to the magnitude of the roll error. However, this alone won't keep the vehicle upright indefinitely, because in cases where large disturbances occur, the correction torque can cause the vehicle to build up enough angular momentum that it rolls itself to the opposite extreme before the weight shifter can respond. To account for this scenario, a second input is provided to the feedback loop using the tilt angle of the passive gyroscope. The tilt angle is read by measuring the analog voltage output of a potentiometer connected to the gimbal shaft. This data could also come from the MPU6050 itself, but I thought it'd be interesting to use a direct analog measurement from a mechanical source. The more tricky part of stabilizing the vehicle comes from turns when driving forward. These might actually require a separate control moment gyro for correcting the much larger but short-term accelerations. The whole system is fed by either a 3S or 4S (12V or 16V) LiPo battery to a 620 kV brushless motor for the gyroscope and a 550 RPM dc gearmotor for the drive wheel. +5V DC is provided by an LM2596 buck converter module for the Arduino, RC Reciever, MPU6050 sensor, and servos. The gyroscope flywheel is a 80mm x 16mm brass disc. With a little more development I'm confident that this approach can be used to make a full-scale bicycle self-balancing (and remote control). Previous videos on Gyro stabilization: Passive gyro - one wheel vehicle: https://www.youtube.com/watch?v=XdVXrno-3B4 Control moment gyro stabilized monorail: https://www.youtube.com/watch?v=OpyLmIjZaxY

9MdJLTgTCSU | 09 Oct 2024
Head to https://squarespace.com/hyperspacepirate to save 10% off your first purchase of a website or domain using code HYPERSPACEPIRATE In this video I'll examine the "Autocascade" refrigeration cycle. The Autocascade cycle is a vapor-compression cycle that achieves multiple stages of refrigeration with a single compression. This is done by compressing a high-boiling and low-boiling refrigerant together. In this video, the high-boiling refrigerant is Propane or R290 (-42C at 1 atm) and the low-boiling refrigerant is Ethylene or R1150 (-104C at 1 atm). When the refrigerants are compressed and cooled back to ambient temperature, the high-boiling refrigerant will be liquefied, while the low-boiling refrigerant will still be gaseous. A phase separator uses gravity to separate the liquid from the gas. The liquefied refrigerant falls into a sump at the bottom of the phase separator, which then flows through the expansion valve or capillary tube into an evaporator, then returns to the compressor inlet. When the high-pressure, low-boiling gaseous refrigerant leaves the phase separator, it travels across the cold evaporator, causing it to condense into liquid. The low-boiling liquid refrigerant then travels to its own expansion valve or capillary tube where its pressure drops, causing it to boil and deliver the system's cooling to the load in a second evaporator. The catch is that the compressor has to be able to deliver a very high pressure in order to both condense the high-boiling refrigerant AND pressurize the low-boiling refrigerant enough that it will condense at the low-boiling refrigerant's evaporation temperature. This results in significant compressor heating, and in the case of my system, it had to be run at less than 100% duty cycle to avoid overheating. Here's a few performance figures from the device in this video: Average Power Consumption: 750W High Side pressure: 450 psi (32 BarA) Low Side pressure: 50 psi (4.5 BarA) Ultimate Temperature: -81C Refrigerant: Approximately 110g Propane and 70g Ethylene The main use of this system is to serve as a cold trap in applications that normally require expendable dry ice, such as freeze-drying or condensing certain gases at atmospheric pressure. The example I used here was condensing Ammonia gas to make Anhydrous Ammonia, which is extremely useful for making a variety of compounds. Control Board Schematic: https://drive.google.com/file/d/1NGpC69HgCdLxXWXaIiD8q-F3X98ENsUe/view?usp=sharing Music Used: Kevin MacLeod - George Street Shuffle

15ga4KMSWqU | 21 Sep 2024
Head to https://squarespace.com/hyperspacepirate to save 10% off your first purchase of a website or domain using code HYPERSPACEPIRATE In this video I'll use a steam turbine to generate electricity using a BLDC motor as a generator to create 3-phase alternating current. The turbine is machined from a brass block, with a 2" x 2" x 1" housing and 46mm diameter / 19mm wide rotor. As a nozzle, it has a 1mm orifice. The steam is generated by a flash boiler that's heated with a propane flame and fed from a pressurized water tank. A unique feature about this boiler design is that the feedwater pressurization comes from the propane fuel. The boiler evaporates approximately ~1 gram/sec of water, meaning it's *absorbing* about 2.6 kW of heat. The generator puts out a peak power of 17 watts, making it 0.65% efficient in a best case. In reality, a large portion of the heat is probably lost to the surroundings instead of heating the boiler, so the efficiency is probably even less than that. The average steam pressure right before the nozzle exit was about 60 psi (~4 bar) for the tests in this video. Huge losses were probably caused by the relatively large gaps between the turbine rotor and the housing wall. Also, the lack of a converging-diverging nozzle is probably another source of inefficiency, but I don't think I currently have the ability to machine one at such a small scale. The burner itself was probably drawing in much more air than was neccesary for combustion, meaning a large volume of air was probably just acting as a parasitic load on the burner. The power output of this thing was pretty small, but large enough to charge a phone / tablet or power a small radio, which could actually make it useful in an emergency if nothing else was available. The idea for this turbine is a development on some compressed-air turbine designs i experimented with in two videos published in 2022: https://www.youtube.com/watch?v=Yg5swK_AnbU https://www.youtube.com/watch?v=RMUHxo2TOUk Machining this thing out of metal was a lot of work, so maybe if i make a future video on steam turbines, I'll try one of those Tesla Turbine things, since those just require a big stack of thin plates.
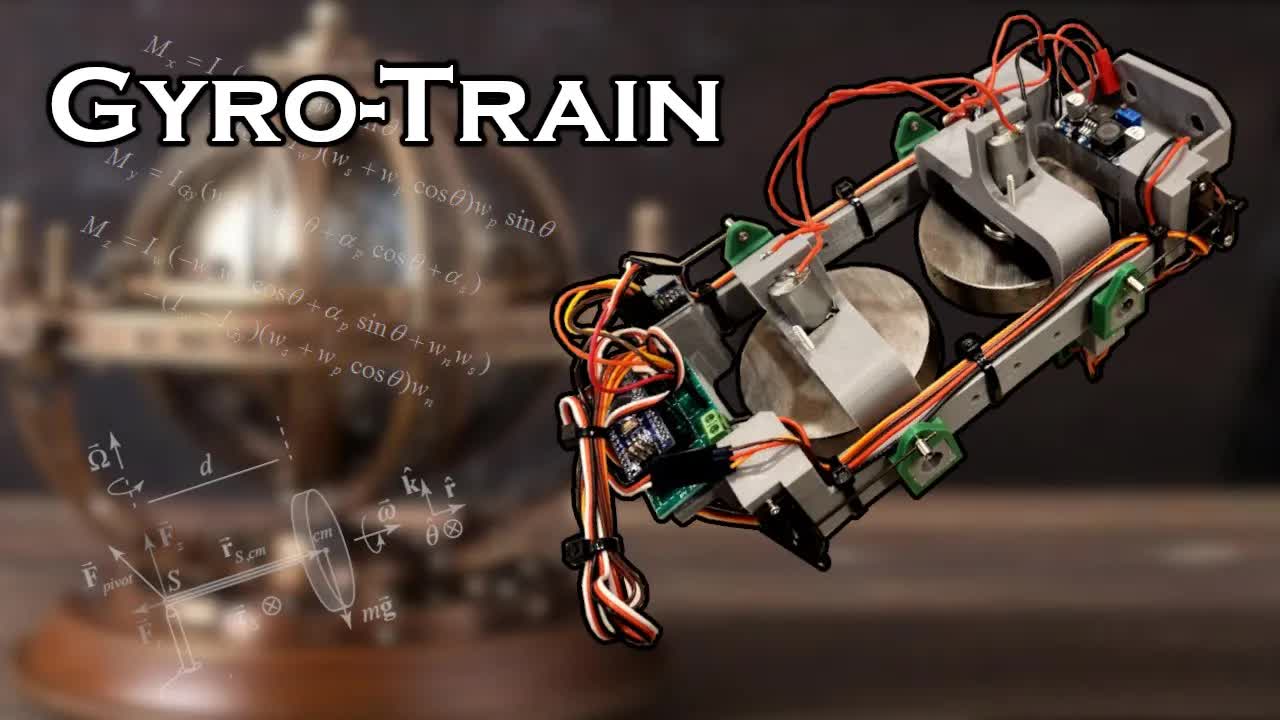
OpyLmIjZaxY | 23 Aug 2024
Head to https://squarespace.com/hyperspacepirate to save 10% off your first purchase of a website or domain using code HYPERSPACEPIRATE In this video I'll demonstrate an example of gyroscopic stabilization of a two-wheeled vehicle by building a model of the 1903 "Gyro-Monorail", which was an experimental monorail train car that used control moment gyros (CMGs) to keep it upright on two wheels. This scheme could also be used for stabilizing a bike or motorcycle, though. The end result is the same as using a reaction wheel, but rather than applying correction torque to a big wheel with a lot of inertia at near-zero RPM, the CMG uses a pair of fast spinning gyros that are tilted back and forth to correct the orientation of the vehicle from gyroscopic torque. The torque produced is a product of the angular momentum of the wheel(s) and the rate of tilt of their rotation axes. In theory this would work just fine with a single wheel, but if the vehicle experiences a change in pitch, that would cause an unwanted tilting effect (same thing as "P-factor" in airplanes). By having a pair of counter-rotating gyroscope wheels spinning at the same rate, any unwanted torque effects are canceled out. In order to produce a net torque, the wheels are tilted opposite to one another, using a pair of RC servos for each wheel. The wheels are 3" x 0.5" solid steel discs that can spin up to 8,000 RPM, but due to excessive vibration, I'm running them at a much lower speed than that. Steel discs probably weren't neccesary for this particular project, and I could have just used 3d printed discs spinning at a higher RPM. An MPU6050 gyro/accelerometer drives the servos via. an Arduino board with a little bit of code on it in order to tilt the CMGs to provide stabilizing torque on the vehicle. This could also be done with an analog circuit, or even purely mechanically, but that's a project that deserves its own video. A tiny gear motor drives one wheel of the train to make it crawl along the track. It moves relatively slowly, but the point of the project is to demonstrate the tilt stabilization, and not neccesarily to move the vehicle super fast. The motors run off a 2-cell lithium battery (approx. 8.0V), while the RC servos, Arduino, and sensor board run off of 5V supplied by an LM2596 buck converter. Even though it's a relatively simple project, the idea of seeing an unstable two-wheeled vehicle keep itself upright seems almost magical, and I'm considering scaling this up to a full-sized adult bicycle. Music Used: Kevin MacLeod - Lobby Time

7M5x2OFYP-k | 13 Aug 2024
Head to https://squarespace.com/hyperspacepirate to save 10% off your first purchase of a website or domain using code HYPERSPACEPIRATE In this video I'm going to show an easy method to extract pure copper metal from copper sulfate and then I'll melt it down and use a homemade CNC mill to machine the castings into parts. In this case, the parts were just decorative, but you could absolutely use this approach to make useful parts too. I had lots of copper sulfate laying around because I like using it to grow crystals, but you may also have some on hand if you do gardening or pond maintenance. Copper metal (Cu) can be extracted from copper sulfate (CuSO4-5H2O) by electrolysis, or by simply inserting a metal into the solution that's more reactive than copper (which is most metals). When this happens, a single-displacement reaction takes place, wherein the copper atom is dropped and the sulfate ion bonds to the other metal, leaving copper dust to precipitate out. The nice thing about dissolving metal this way is that there's no nasty fumes generated as in the case with strong acids or bases. Copper sulfate pentahydrate is 25.4% copper metal by mass, and sells for around $2/lb in the US, so if you neglect the cost of the scrap metal, that comes out to $8/lb of copper metal, which isn't too far above the the cost of copper scrap at the time of publishing this video, which is $5-7/lb in the US. As a bonus, if you used electrolysis instead of dissolving scrap metal, you'd be left with sulfuric acid after extracting the copper, which is useful on its own. The fine copper dust that precipitated out oxidized pretty quickly when I dried it, so in my first attempt to melt it, it just stayed oxidized and didn't liquify. When I mixed brazing flux powder in with the copper powder, I did succesfully manage to melt it. In total I chemically produced and melted a little over 1kg of copper for this project. Parts were cut on my CNC mill with a 1/8" end mill traveling 8mm/sec with a 0.1mm cut depth, although i later reduced that to 0.05mm because the mill isn't rigid at all, so that's something I'll need to fix in the future. It works pretty well on aluminum and brass, but struggled quite a bit with copper. Since both parts were decorative, I aged one of them by exposing it to Ammonia fumes for several days, causing deep blue copper hydroxide to form on the surface, which made it look like some sort of ancient artifact. I also experimented with fumes from Sulfuric Acid, Nitric Acid, Acetic Acid, and Hydrochloric Acid for aging, but I think Ammonia fumes gave the best appearance. In most cases this probably isn't a very practical project, but I thought it was pretty interesting to go through the process of transforming a blue liquid into solid metal parts. Music Used: Kevin MacLeod - Lobby Time Kevin MacLeod - Hard Boiled
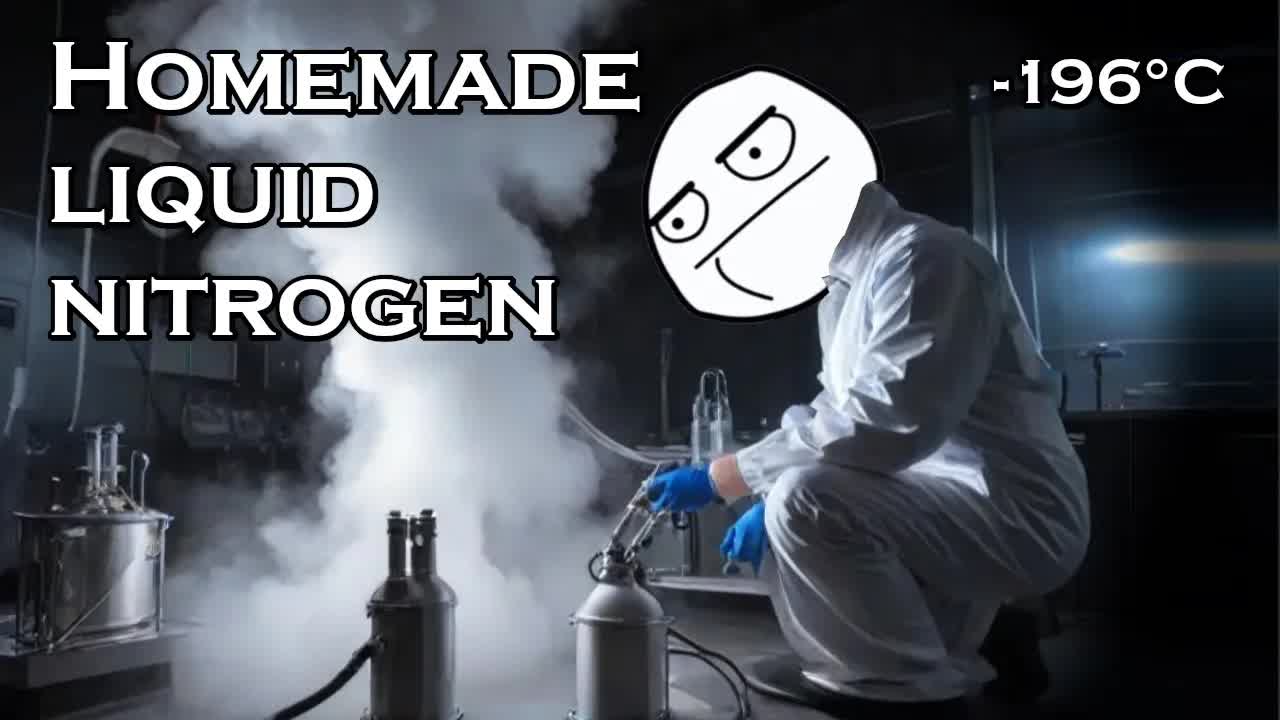
eqxwsfy72L0 | 15 Jul 2024
Head to https://squarespace.com/hyperspacepirate to save 10% off your first purchase of a website or domain using code HYPERSPACEPIRATE In this video, I'll show how I built a cryocooler out of salvaged air conditioner parts that's able to make liquid nitrogen at -196C. The system operates on a process known as the Mixed-Gas Joule Thomson cycle. A mixture of refrigerant gases are compressed, cooled to ambient temperature, and then expanded inside a long counterflow heat exchanger. When the gases expand, they cool. Cold, low-pressure gas cools the incoming high-pressure gas causing it to drop its temperature even further, creating a snowball effect that drives the cycle down to cryogenic temperatures. The lowest temperature I've achieved is -180C with a 30/70 mixture of Propane and Argon. For higher performance, a separate vapor compression system is used to pre-cool the gas mixture to around -30C before it enters the regenerative heat exchanger. This adds complexity, but nets a performance gain, since total cooling power goes up by 30-50% with only a 15-20% increase in energy consumption. The super cold gas travels through a heat exchanger pipe in a small tank. High pressure nitrogen is pumped into the tank at up to 30 bar and liquefies at around -150C. Once the tank is filled with liquid nitrogen, it's discharged through an electronic expansion valve at the bottom of the tank into a thermos or dewar. This is different from the pure-gas joule thomson cycle in which nitrogen is expanded from 200-300 bar to atmospheric pressure to create a cooling effect. In the mixed-gas cycle, the refrigerant gases and the process gases being liquefied are two different streams. The gas mixture being used is: 25% Propane 15% Ethylene 20% Methane 20% Argon 20% Nitrogen The typical operating pressure is 400 psiG on the high pressure side and about 20 psiG on the low pressure side. Power consumption is approximately 1.4 kW, and my current production rate is about 130cc/hour of liquid nitrogen, though I'm confident this can be improved close to 300cc/hour with some adjustments. The current energy cost is about $1.29 per liter produced. For this video I've used nitrogen gas from a tank I purchased, but in a future video I'll show the process of separating out oxygen/nitrogen. Music Used: Kevin MacLeod - Groove Groove Kevin MacLeod - George Street Shuffle

4rjwx5q2fVI | 14 May 2024
To try everything Brilliant has to offer for free for a full 30 days, visit https://brilliant.org/HyperspacePirate/ . You'll also get 20% off an annual premium subscription. In this video I'm going to Liquify Methane / Natural gas with my Mixed-Gas Joule-Thomson Cryocooler. Methane liquifies at -162C under ambient pressure, but at elevated pressures, it can be condensed as high as -85C. In this experiment I'll condense some at -118C / 12 bar of pressure. My cryocooler was meant for making liquid air or liquid nitrogen, but I figured I'd try liquefying some methane along the way to see if there's any pitfalls / issues with making liquefied natural gas (LNG), which there definitely were. The joule-thomson cycle works by compressing gas and then expanding it, which forces it to drop its temperature. By back-flowing the cold low pressure gas back over the high pressure gas in a counterflow heat exchanger, the cryocooler creates a positive feedback loop that drives the temperature down into the cryogenic range. The lowest temperature I recorded was -180C. Using pure methane or pure nitrogen would require hundreds of atmospheres of pressure in the cycle to reach the desired temperature, but by using a mixture of gases with different boiling points (similar to an "autocascade" refrigeration system), the same effect can be achieved at just 20-30 bar which a repurposed air conditioner compressor can handle without any problem. For liquefying Methane, a gas mix of Propane, Ethylene, Methane, Argon and Nitrogen is used. The same components are used for liquefying Nitrogen, but in different proportions to optimize heat lift at lower temperatures. If you want to learn more about the joule-thomson refrigeration cycle, check out my previous videos on the subject: https://www.youtube.com/watch?v=r_B0RmRlFHA https://www.youtube.com/watch?v=7uQ3YW3_3eA Liquid Methane / LNG is becoming used more frequently both for power generation and vehicles because it has an energy density similar to gasoline/diesel/kerosene, but is extremely easy to ignite/burn and burns very clean. In the near future, hardware will be delivered to the moon via LNG-burning rockets (starship). At the hobby level, I don't see much use for it, but it's a fun science experiment since this is technically the first cryogenic liquid I've produced. Music Used: Mining by Moonlight - Kevin MacLeod Backbay Lounge - Kevin MacLeod Apero Hour - Kevin MacLeod George Street Shuffle - Kevin MacLeod

oI_QEbG6mDE | 11 Apr 2024
To try everything Brilliant has to offer for free for a full 30 days, visit https://brilliant.org/HyperspacePirate/ . You'll also get 20% off an annual premium subscription. This is part III of my video series on building a DIY vapor-compression casacade (i.e. multi-stage) refrigeration system. In the last two videos, i demonstrated the concepts needed to make a cascade system work and reached temperatures below -110C, but because i used low-powered reciprocating compressors meant for R600A, I wasn't able to build a system that ran continuously and only managed to evaporate low-temperature refrigerants in short bursts. This time, I'm using a pair of rotary compressors extracted from 5,000 BTU window air conditioner units. The first stage will use propane (R290) as a refrigerant, and the second stage will use Ethylene (R1150). The compressors were made for R410A, so they're able to run as high as ~30 bar continuously without a problem. This will allow me to condense Ethylene at the first stage evaporator temperature of around -20C to -25C. To extract more efficiency (and a lower temperature) out of the system, I use subcoolers on both stages; the return lines to both compressors are wrapped in capillary tubing coming from the condensers. The lowest temperature I managed to achieve with this system was only -88C, but that's probably because I ran the second stage suction pressure relatively high (around 4-6 bar) in order to keep the mass flow rate high. Down to about -63C, the efficiency or "coefficient of performance" (COP) is about 10%, so there's definitely some room for improvement. The best way to improve the ultimate temperature and/or thermal efficiency of this system would be to use a sub-cooler with a thermal gradient across it that looks basically identical to the regenerative heat exchanger in a joule-thomson system. When I experimented with this using my precooled joule-thomson cryocooler with 100% ethylene (effectively turning it into a cascade vapor compression system), I achieved nearly twice the thermal efficiency of the device I built for this video. I originally planned to use this system to liquefy Methane. This is possible at -88C, but would require a very high pressure, and with the marginal cooling power at that temperature, it's probably not practical, so I'll be doing that in my next video using my joule-thomson cryocooler. I'd also recommend using a higher-boiling refrigerant for the second stage - like R508 (if you can get it), Ethane (R170), Nitrous Oxide (R744A), or even Carbon Dioxide (R744) (although CO2 is only feasible if you keep the second stage evaporator ABOVE the -56C). The boiling points of Ethylene and Propane are far enough apart that the system is reaching pretty far. Music Used: Kevin MacLeod - George Street Shuffle Kevin MacLeod - Bossa Antigua Kevin MacLeod - Lobby Time Kevin MacLeod - Elevator

zRrgvYJ8gAY | 02 Mar 2024
Head to https://squarespace.com/hyperspacepirate to save 10% off your first purchase of a website or domain using code HYPERSPACEPIRATE Original Ethylene production video: https://www.youtube.com/watch?v=UKFEbYdKdJg Board Schematic: https://drive.google.com/file/d/1jGZg0plUJJzqGkXVEZyQ5Ky7ZHtwXC8n/view?usp=sharing Arduino Code: https://drive.google.com/file/d/12d2MGy-z9415vCw4UUFIL6S_Q7bAi6pA/view?usp=sharing In this video I'll show how I automated the process of producing Ethylene (C2H4) gas for use as a refrigerant. Ethylene is known as Ethene, but is different from Ethane which is C2H6. My original process used a manually controlled flame from a propane burner to heat a catalyst pipe full of aluminum oxide to decompose ethanol vapor into Ethylene and water vapor and fill a beach ball with the Ethylene gas, which I'd later pump into a tank under pressure. This process was time consuming, inefficient, and required constant attention to keep the flame at the right level to maintain temperature. I use a lot of Ethylene gas to test refrigerant mixes for my cryocooler, so it was worth the time to make the process hands-off. The new catalyst pipe is a 1-3/8" x 24" aluminum tube with 8 135W band heaters clamped to it. 1/4" aluminum tubes are brazed to the catalyst pipe to serve as the inlet / outlet. The band heater section is insulated to maintain temperature, but the ends of the pipe are exposed to keep them cooler to avoid melting the aluminum brazing alloy. The temperature of the catalyst pipe is controlled by a PWM signal from an arduino to a solid state relay driving the band heaters, with feedback from a thermocouple in the middle of the pipe. The target temperature I used in this video was 450C. Lower temperatures will make a higher percentage of Diethyl Ether, and higher temperatures will create Hydrogen and Carbon, and possibly damage the catalyst pipe. The ethanol vapor is supplied by a 1L boiler which is quickly brought up to its boiling temperature with a 100W heater and then sustained by a 30W heater. Feedback for the boiler heater control is provided by a thermistor inside the boiler. If the temperature inside goes over the boiling point of the ethanol, the program assumes the liquid has been depleted, and shuts off. The average production rate of Ethylene gas is around ~40L/hr depending on the temperature used for the reaction. One issue i ran into early on was that I used denatured alcohol from the hardware store, which i discovered was up to 60% methanol. This still creates Ethylene, but it also creates several other Alkenes from CH2 chains. I solved this problem by using Bio-ethanol, which appears to be azeotropic 96% ethanol without additives. The ethylene is automatically pumped into a pressure tank when the gas pressure pushes up the piston of a 500 ml syringe until the piston trips a limit switch that triggers a compressor to turn on. At the time of this video's making, I've created nearly 1,000L of ethylene gas, a lot of which i've liquefied for cryogenic experiments. Later, this gas will be filtered, dried, then used as refrigerant in a cascade vapor compression system, and as a component in my mixed- gas joule-thomson cryocooler. Music Used: Kevin MacLeod - Bossa Antigua Kevin MacLeod - Lobby Time Kevin MacLeod - George Street Shuffle

C3LCjp_REYA | 07 Feb 2024
Head to https://squarespace.com/hyperspacepirate to save 10% off your first purchase of a website or domain using code HYPERSPACEPIRATE In this video I'll show how to make Ethane gas (C2H6), also known as refrigerant R170. This is the slightly heavier cousin of Ethylene or "Ethene" which is C2H4 (Refrigerant R1150). Ethane has a boiling point of -88C compared to Ethylene's -104C. The main motivation behind synthesizing Ethane was to have a refrigerant for the second stage of a cascade vapor compression system that could still reach ultra-low temperatures, but without as high of a pressure demand. Assuming a heat exchanger temperature of -20C on the first stage of a cascade system, it would take 25.3 bar or 352 psi to condense Ethylene, whereas Ethane would only require 14.2 bar or 191 psi. This means that a small system using the relatively weak reciprocating compressors from a mini-fridge or tabletop ice-maker could use Ethane for a second stage, whereas Ethylene would typically require a rotary compressor to handle the higher pressure. Industrially, Ethane is produced from crude oil or by hydrogenation of Ethylene. The hydrogenation reaction occurs by passing Ethane and Hydrogen over a high temperature nickel catalyst. In theory this process could be done by an amateur/hobbyist, but there's actually a simpler method - electrolysis. When an acetate solution undergoes electrolysis with a platinum anode (whether acetic acid, or some acetate salt), the acetate ions break up into Carbon Dioxide (CO2) and Ethane (C2H6), in a process known as Kolbe electrolysis. This is actually a pretty complicated process that involves a lot of organic chemistry that I don't understand - but it works. In this video, I'll use Sodium Acetate as my electrolyte. Theoretically, straight Acetic Acid (or vinegar) can be used, but its electrical conductivity is extremely low, so Sodium Acetate is a better option. Over time, as the acetate ions are consumed, the Sodium Acetate becomes Sodium Carbonate, causing the solution to become basic (pH over 7.0). Once this happens, the Kolbe electrolysis process stops, and regular alkaline water electrolysis occurs, producing oxygen gas at the anode. For this reason, the electrolyte needs to be made with a generous excess of acetic acid, and the reaction should be stopped if the cell pH goes above around 6-7. Since the gas output contains CO2, it has to be scrubbed with Calcium Hydroxide in order to extract the pure Ethane. I also included a dessicant canister in line with my scrubber, since the gas has a significant amount of moisture in it. To demonstrate its refrigeration properties, I compressed my Ethane into a ~100cc pipe in an ice bath to force it to liquify, then discharged it through a valve. When the liquid Ethane is brought down to 1 atmosphere, it flashes to vapor and drops its temperature to -88C. One additional advantage of Ethane over Ethylene is that it can be stored in liquid state at room temperature, since its critical point is 32C. At 25C, liquid Ethane has a pressure of 41.9 bar or 593 psi, so it could easily be stored in a tank meant for CO2 or Nitrous Oxide, which have much higher pressures in their liquid state at room temperature. Link to Ethylene Synthesis video: https://www.youtube.com/watch?v=UKFEbYdKdJg Music Used: Kevin MacLeod - Bossa Antigua Kevin MacLeod - Lobby Time Kevin MacLeod - Groove Groove Kevin MacLeod - George Street Shuffle Kevin MacLeod - Hard Boiled

f6mLykQjxZ0 | 08 Jan 2024
Head to https://squarespace.com/hyperspacepirate to save 10% off your first purchase of a website or domain using code HYPERSPACEPIRATE In this video I'll be showing how to produce mild refrigeration with compounds extracted from urine. Human urine contains 1-2% urea (CO[NH2]2), which I'll be convert into Ammonia (NH3). This can be done either by thermal decomposition of solid urea after it's been distilled out of urine, or by reacting urine with sodium hydroxide (NaOH) and heating it. I opted for the second method, since it's less energy intensive. Videos showing the extraction of ammonia from urine often concentrate the urine by a factor of 10-20 before adding sodium hydroxide, but I found this method to be too time consuming and liable to overflow from excessive foam. Instead, I found it worked best to simply react un-concentrated urine with sodium hydroxide and heat it. Also, the smells produced from this approach are relatively mild. The only downside is that numerous batches of urine need to be processed. Once Ammonia is obtained, there's several ways it can be used for refrigeration. Anhydrous ammonia can be used as the refrigerant in a vapor-compression system and has a temperature/pressure and phase behavior almost identical to propane. Aqueous ammonia can be used in a heat driven vapor-absorption system, and Ammonium Nitrate (NH4NO3) can be used as a "cold pack" by endothermic dissolution in water. In this video I'll be using the third method, because I wanted to investigate a heat-driven refrigeration system, and endothermic dissolving seemed like a simpler approach than vapor-absorption. The Ammonium Nitrate is produced by reacting it with Nitric Acid (HNO3). I produced the nitric acid by the "Birkeland-Eyde" process, which uses a high voltage arc to ionize oxygen and nitrogen in the air, after which a certain percentage of those atoms recombine to form Nitric Oxide (NO) gas. The nitric acid quickly combines with more oxygen to form Nitrogen Dioxide (NO2), which is bubbled through distilled water. When Nitrogen Dioxide interacts with water, it forms Nitric Acid. This is a very slow and energy intensive process, but has the advantage that it allows the production of nitrates quite literally out of thin air. I should note that in small quantities, Ammonium Nitrate is actually pretty safe to store and handle, and even if it's heated directly with a blow torch, it just melts and then decomposes into Nitrous Oxide (N2O) and water vapor. To produce refrigeration, the ammonium nitrate is dissolved in water in a thin-walled aluminum can and placed into contact with a large water reservoir inside a foam container. The water reservoir acts as a thermal reservoir. Once the solution has absorbed as much heat as it can from the water reservoir, it's removed and then recharged by boiling off the water, cooling in a water bath, and then adding new water into the dry salt. In theory this works pretty well, but in reality i found that the boiler didn't work fast enough to keep the fridge temperature dropping, so really there need to be multiple cans on a rotation for this to work well. By creating a saturated solution of aqueous ammonium nitrate, I was able to produce a temperature drop to near freezing (about 3.8C) in an aluminum bottle, but only reached a minimum temperature of 13.5C in the fridge. Pretty poor performance, but at least I was able to cool off a soda a little bit. I also tested a few other substances to act as "instant cold" packs by mixing saturated solutions, and these are the temperature drops I recorded: Sodium Chloride: -1.6 C Potassium Nitrate: -11.1 C Potassium Chloride: -13.1 C Sodium Nitrate: -16.4 C Ammonium Chloride: -17.0 C Urea: -19.6 C Ammonium Nitrate: -20.4C Music Used: Kevin MacLeod - Lobby Time Kevin MacLeod - Hard Boiled Kevin MacLeod - George Street Shuffle Kevin MacLeod - Groove Groove

JN_7KgdB1V8 | 05 Dec 2023
Get Surfshark VPN at https://Surfshark.deals/HYPERSPACEPIRATE and enter promo code HYPERSPACEPIRATE for a Holiday Special offer of 5 extra months for free with the Surfshark One package! In this video I'm going to turn seashells into dry ice. Sea shells are mostly made up of limestone - or Calcium Carbonate (CaCO3), which can be decomposed into Calcium Oxide (CaO) and Carbon Dioxide (CO2) when heated to around 900C. I used a 500W induction heater i built to heat a sealed pipe full of sea shells to a hot enough temperature and collected the CO2 gas into a beach ball by using a vacuum pump to extract it from the pipe. For limestone decomposition to occur at a reasonably fast rate, the temperature really needs to be over ~1000C, so this process took several hours (even for only ~50 grams of limestone) and required a vacuum pump to pull off the CO2. I broke down the remainder of my sea shells by dissolving them in vinnegar, and saved the Calcium Acetate biproduct for later use as a solid fuel for camping/hiking. Once I collected a decent volume of CO2, I used a refrigeration compressor to pump it into a plate-stack heat exchanger and used a propane-based vapor compression refrigeration system to chill the high pressure CO2 down to about -30C, so it required only modest pressure to liquify. The refrigeration system is actually the pre-cooler stage for my joule-thomson cryocooler, which i borrowed for this video. Once a decent mass of CO2 has been pumped into the heat exchanger and liquified, it's discharged through a ~1mm diameter capillary tube into a thermos with a glass wool baffle to stop high speed gases from carrying away tiny particles of the ice. With a little bit of improvement to the limestone furnace temperature, and some minor tweaks to my refrigeration system, this could be an extremely cheap way to make dry ice, assuming a limestone source is available. With the right setup, costs could be as low as a few cents per pound of ice. Induction Heater Schematic: https://drive.google.com/file/d/1WWGMMiXeocOpjPDXXiNxOdZxMykq30Rp/view?usp=sharing Music Used: Kevin MacLeod - George Street Shuffle Kevin MacLeod - Groove Groove Kevin MacLeod - Lobby Time

udIEGE5mfcA | 20 Nov 2023
In this video I'll explain how a Magnetron works, collect some current/voltage numbers on a typical household magnetron from a microwave oven, and show how to power one off a 12V battery. Typical DIY magnetron videos only show how to remove the transmitter from the microwave oven and run it with its original circuitry off mains power. Here, I'm basically building a high frequency inverter circuit to run off DC so that the entire device is portable. To do this, I have a ZVS oscillator driving a transformer primary, and the secondary coil is connected to a voltage doubler / rectifier to provide about 3.6 kV DC. There's also a low voltage / high current winding on the transformer to provide power for the Magnetron cathode filament. One of the biggest frustrations of this project was trying to deliver enough current to the Magnetron cathode filament with my ZVS flyback transformer. It took a lot of messing around until i discovered that the filament has some RF chokes in series with it, giving it about 2.8 uH of inductance. At 40 KHz, this inductance resulted in too much impedance for enough current to flow. Fortunately, the fix was as simple as adding about 7 uF of capacitance in series with the filament to cancel out the inductive reactance. With a proper waveguide, the microwaves could theoretically be focused into a relatively narrow beam, due to their small wavelength. However, that's a project in and of itself, which I'm not going to tackle in this video. Output power of the 12V circuit in this video is only around 50-60W, but it can easily be increased by using a larger capacitor value in series with the voltage doubler on the transformer output. Be sure to use metal shielding around yourself and valuable electronics if you do this. Schematic Link: https://drive.google.com/file/d/1MyQgRyLYlGqkrFBLRWcR7STFDM9IlVSg/view?usp=sharing Music Used: Local Forecast - Elevator Kevin MacLeod - Bossa Antigua Kevin MacLeod - Lobby Time Topher Mohr and Alex Elena - Fortaleza

oIWgzVaGn4Y | 04 Oct 2023
In this video I'll show how I built my Hydrogen gas generator using electrolysis of a 10% Sodium Hydroxide solution with 316 stainless steel electrodes. Unlike an "HHO" generator, this cell separates the hydrogen from the oxygen, so it can be collected in a tank for later use. In the video, I demonstrate its usefulness as a lifting gas for a camera-carrying balloon, but my ultimate goal is to liquify it with a cryocooler at -252C or use it as a working fluid in a stirling cycle to serve as a cheap and plentiful substitute for helium. I'm also interested in using it to manufacture synthetic methane by combining it with CO2 in a process known as the Sabatier reaction. The theoretical voltage required to separate water by electrolysis is 1.23V, but in reality it will end up being 1.5-2.0 volts, depending on the electrolyte and electrode chemistry, as well as cell temperature. In order to maximize efficiency and minimize the occurance of heating and side reactions, the voltage on a cell should be kept as low above this threshold as possible. Most industrial devices have a cell voltage somewhere between 2.2-2.5 volts. The efficiency of electrolysis is approximately the threshold voltage divided by the cell voltage. The calculation to approximate hydrogen production rate is: Liters per hour = V_threshold * Current * 3600 / 287,000 * 24 The production rate of oxygen gas is half this amount. One potential pitfall of hydrogen storage in pressure vessels or use as a working fluid in cryocoolers / heat engines is the tendency for atomic hydrogen to work its way into the crystal lattice of metals and cause it to become brittle, similar to how adding carbon to steel makes it more brittle. Supposedly this can be mitigated by ensuring the hydrogen gas is totally dry, and aluminum / copper seem to be far less affected by this issue than steel. It's important to remember that if you're using stainless steel electrodes, over a long period of time, they can degrade and release toxic chromium salts into the electrolyte, some of which may be the hexavalent (Cr6+) form of Chromium. This electrolyte can't be dumped down the drain. To dispose of it properly, you need to evaporate the water and deliver the precipitate to a hazardous waste disposal site. Aqueous solution conductivity chart: https://pdfs.semanticscholar.org/cbc5/22cf4c5e6e690ca48984314c231f6643ee81.pdf Music Used: Fortaleza - Topher Mohr and Alex Elena

7uQ3YW3_3eA | 10 Sep 2023
In this video, I'll build on my progress from the last Joule-Thomson cryocooler video and reach a temperature of -153C on a single stage using parts sourced from window A/C units and common/cheap substances as refrigerants (a mixture of Propane, Ethylene, and Methane). This temperature is low enough to condense any gas except for Hydrogen, Helium, or Neon, at the following pressures: Nitrogen - 25.3 barA (352 PsiG) Air - 20.2 barA (278 PsiG) Oxygen - 10.3 barA (135 PsiG) Methane - 1.9 barA (13 PsiG) I tested several different mixtures to achieve this temperature, but the best performing I've found so far has been a 30/20/50 blend of Propane, Ethylene, and Methane, respectively. The Propane comes from an ordinary grilling tank, the Ethylene is produced by heating denatured alcohol over a catalyst, and the Methane comes from residential natural gas. All these sources are very cheap. For a throttling valve to achieve the Joule-Thomson effect, I use a 1m long 1mm ID capillary inline with a computer-controllable electronic expansion valve (EEV) used for fine-tuning flow resistance. I avoid using *only* an EEV due to the relatively large thermal conduction losses experienced through the bulky metal valve body. The system is charged with 180 PsiG (11.3 BarA). With the EEV wide open, the high/low side pressure is ~400/65 psiG (28.6/5.5 barA) respectively. With the EEV closed as far as possible without shutting off the flow, the high/low side pressure is ~520/10 psiG (36.9/1.7 barA) respectively. A temperature drop of 20-35°C across the EEV+capillary restriction is typical. I use a vacuum enclosure to thermally insulate the cold end of the system, but since I can't reach a vacuum much higher than about ~2 mBar, the vacuum isn't a very effective insulator, so I still had to pack the enclosure and wrap the heat exchanger coil with glass wool. Research papers on this subject claim pressures on the order of 10^-4 mBar inside the vacuum enclosure, which I'm unable to produce. While the temperature I've achieved is low enough to make liquid nitrogen / oxygen / methane under pressure, the heat exchanger I assembled to do so on the cold end was ineffective, so I didn't liquify any gas in this video. In the next part of this series, I'll focus on mixture optimization (by adding varying percentages of Butane and Nitrogen or Argon to the mix), increasing cooler power / temperature drop by use of a pre-cooler, and construction of a cold head that incorporates a large "reservoir" for accumulating several hundred CC of liquified gas before discharge to atmospheric pressure. If this project is succesful in producing decent quantities of liquid Nitrogen, I'll turn my focus toward production of Liquid Hydrogen using a Joule-Thomson system with LN2 pre-cooling.

-qWQaX8_EDY | 21 Aug 2023
In this video I'll attempt to build a Cloud Chamber for visualizing subatomic particle trails. These particles come primarily from cosmic rays, which is ambient radiation from outer space. The three main sources of radiation we'll see here are Alpha particles (relatively slow but massive helium nuclei), Beta particles (very fast electrons, but much lower mass than Alpha particles), and Gamma rays (an ultra high energy photon with frequencies in excess of 10^19 Hz, which is about 100,000x the frequency of visible light). In the chamber, alcohol evaporates from either a reservoir, or more commonly, a fibrous object with large surface area like a sponge / towel. The vapor pressure of the alcohol inside the chamber reaches saturation (like 100% humidity, but with alcohol vapor). When a plate at the bottom of the chamber is cooled, it drives the vapor below the its condensation temperature (same thing as moist air hitting the dew point). However, when this happens, the vapor doesn't immediately condense because it needs a nucleation site, so it's in a semi-unstable state where the moment it contacts something, it'll condense. When a high energy particle flies through, it smashes into the alcohol molecules, creating a nucleation site along its flight path. This leaves behind condensation trails, similiar to a jet aircraft. If the trails are illuminated with an intense light source against a black background, they can be clearly seen with the naked eye. Alpha particles show up as short, fat trails. Beta particles show as thin lines that often have a dashed/dotted appearance, and Gamma Rays / X Rays show up as thin squiggly lines. Also, the paths of Alpha and Beta particles can be influenced by a magnetic field because they're charged. The charge/mass ratio of the Alpha is too low to cause any noticable deflection, but with a strong enough field, a beta particle can be steered into a spiral path. Unfortunately, I wasn't able to do this in my build, even with a large N52 magnet. The most dramatic displays occur when a piece of radioactive material is placed in the chamber. In this video, I used an old camera lens containing Thorium-232 as a radiation source. For this chamber, the plate is cooled to about -25C with a vapor compression system. The compressor, condenser, and filter/dryer come from a used icemaker i bought off eBay for $40, emptied, and backfilled with propane from my grill. The evaporator is a coil of 1/4" copper tubing thermally anchored to an aluminum plate with silicone. With the condenser fan, the whole system uses about 1.6A at 115V, or 172W. This is dramatically more powerful, efficient, and reliable than a peltier cooler based system, but requires some basic brazing and a vacuum pump to empty the refrigerant lines. For alcohol, I use 99% Isopropyl, but Ethanol or Methanol can also be used. I tried acetone for its lower boiling point, but it never produced any visible particle trails. The application of a vertical electric field with several thousand volts will "sharpen" the picture of the trails by "flushing" residual ions out of the fog layer. However, mine wasn't very effective, probably because I only used a loop around the chamber walls instead of a grid covering the entire upper surface. Music Used: Kevin MacLeod - Lobby Time Serge Pavkin - Cosmic Glow I also have a patreon now if you want to help support the channel. This makes it a lot easier for me to buy parts and equipment for these projects: https://www.patreon.com/HyperspacePirate
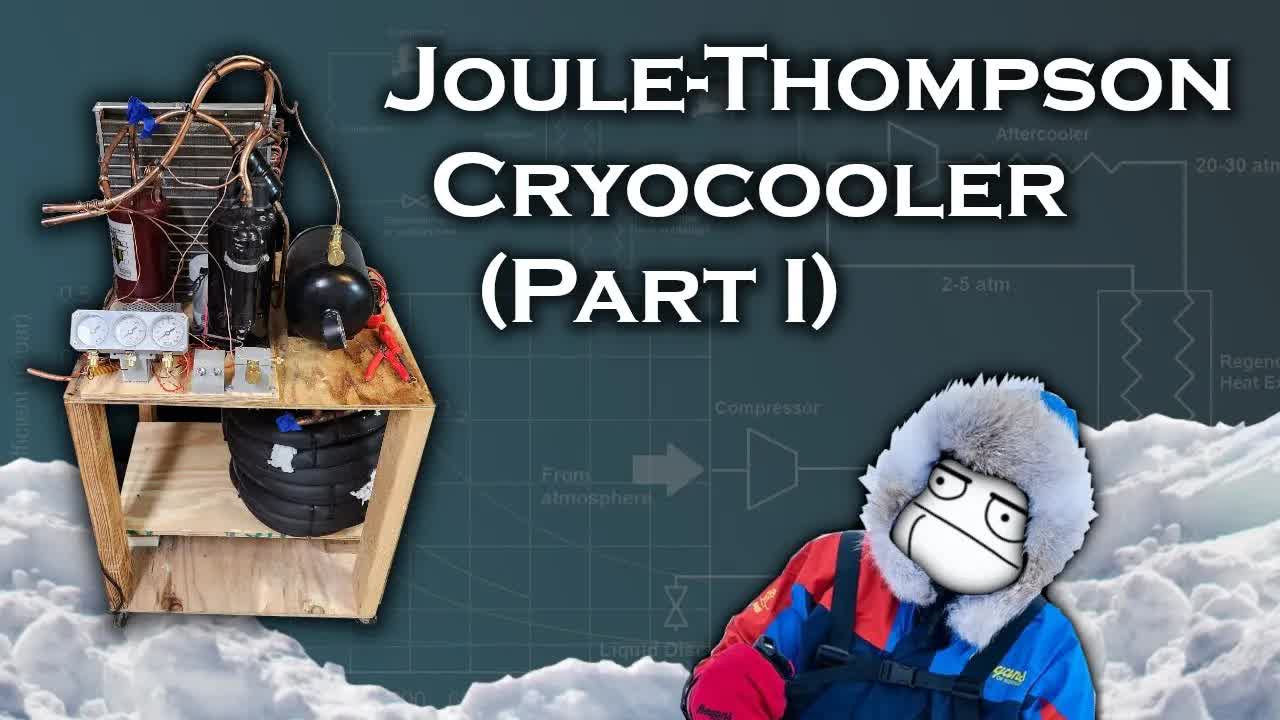
r_B0RmRlFHA | 03 Jul 2023
Big thanks to @Exotic_Chem_Lab chem lab for sharing his experience to help make this project happen In this video I'm going to examine the performance of a homemade cryocooler using the joule-thompson effect. A joule-thompson type device was the first method that was used to liquify nitrogen on an industrial scale, but it was very inefficient. Using nitrogen at pressures of 200-300 bar, it would drop the temperature through a regenerative heat exchanger until it reached a low enough temperature that some of the nitrogen would condense to liquid when it expanded through a flow restriction. This process was very inefficient, usually less than 1% of input power went into actually cooling and condensing the nitrogen. I'm going to be taking a slightly different approach that's a sort of half-way between a joule-thompson device and a vapor compression system. Instead of using air or pure nitrogen as a working fluid, I'm going to use a mixture of hydrocarbon gases (propane, ethylene, and methane), which have dramatically higher joule-thompson coefficients. Unlike a traditional joule-thompson system, this type operates in a closed-loop. Typical low side temperatures get down to -160C to -170C, which is enough to liquify air or pure nitrogen if it's pressurized to 10-20 bar inside the cold end, which is trivial to do. Higher boiling gases will condense as the temperature of the cold head is reduced and cease to contribute to the joule-thompson cooling, but still make a major contribution to heat transfer when they evaporate in the regenerative heat exchanger. I built this system using the compressor and condenser coil from a 12K BTU portable AC unit (meaning the compressor pulls around 900W loaded). The oil separator is a temprite 900 series, and the heat exchanger consists of 30 ft (9m) of two 3/16" tubes for the high pressure side and a single 5/8" tube for the low pressure return line. I only reached -88C in this video, because a defective oil separator was causing oil to overflow into my heat exchanger and freeze at such low temperatures, resulting in clogs in the capillary tube. The heat exchanger also wasn't properly insulated or pre-cooled in this video. With those changes, reaching -150 to -160C should be relatively easy with the correct gas composition. Music Used Kevin MacLeod - George Street Shuffle Kevin MacLeod - Groove Groove Kevin MacLeod - Lobby Time Local Forecast - Elevator
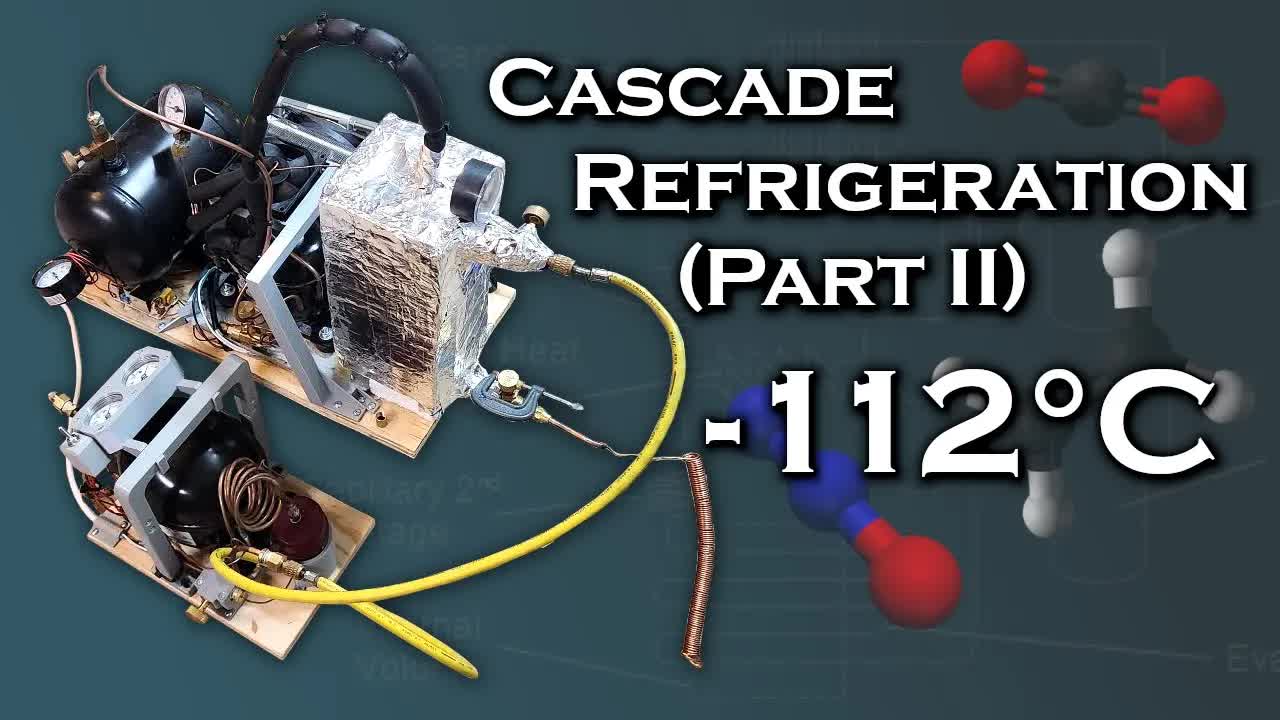
JSjlcPMi2yA | 11 Jun 2023
This is the second part of my video series on building a DIY cascade refrigeration system, where i reach (and exceed) my goal of reaching -100C. Part I: https://www.youtube.com/watch?v=T76UDLPv04Y In this video, i experiment with some alternative refrigerants for second stages. I tried CO2 (R744) (which isn't viable due to freezing) and Nitrous oxide (R744A), which is a very effective refrigerant but also potentially hazardous. I reached an open-cycle temperature of -81C with CO2 and -91C with Nitrous oxide. Later, i figured out that the source of my hydrogen contamination in my Ethylene production wasn't from excessively hot aluminum oxide catalyst, but rather from an excessive flow rate of ethanol. There was more ethanol flowing than the catalyst could decompose in a given timeframe, and when the unreacted ethylene (which was superheated) came into contact with the copper tubing feeding the condenser, it decomposed to form acetaldehyde and hydrogen. This was the primary source of contamination. To remedy this, i built a new ethanol boiler consisting of a well insulated 250ml flask with a load resistor placed inside. The load resistor was powered by a bench power supply which allowed precise control of the ethanol flow rate. The reactor works best with under 40W into the boiler. This is low enough to ensure the catalyst can handle all of the Ethanol. I also removed the copper lines in the reactor and replaced them with aluminum to eliminate any possibility of having copper-catalyzed decomposition that would create hydrogen. The lowest open-cycle temperature i achieved with Ethylene was -112C, exceeding my original goal for this project of -100C. It's possible to build a cascade refrigeration system to reach liquid nitrogen temperatures, but excessively complicated to the point of not being practical, since it would require 4 stages to work. The next phase of this project will focus on Joule-Thompson type cooling, but instead of using pure nitrogen or air, I'll be using a mixture of Propane, Ethylene, Methane, and Nitrogen. If optimized, this scheme can exceed the performance of a conventional Joule-Thompson cryocooler by an order of magnitude, while only requiring modest pressures (20-30 bar) compared to the 200+ bar normally needed. Once again, big thanks to Exotic Chem Lab for sharing his experience in DIY refrigeration and cryocooling to help this project succeed: https://www.youtube.com/@Exotic_Chem_Lab Music Used: Kevin MacLeod - Lobby Time

T76UDLPv04Y | 14 May 2023
Big thanks to Exotic Chem Lab for providing lots of guidance / info on this project. Check out his channel at: https://www.youtube.com/@Exotic_Chem_Lab In this video I'll be building on the work I did in my last 2 videos (DIY vapor compression refrigeration & Ethylene Production) to create a 2-stage or "cascade" vapor compression refrigeration system that uses propylene (aka MAPP gas) in the first stage, and Ethylene (R1150) in the second stage. The goal of the project is to hit -100C. A major snag i ran into was that I wasn't getting the temperature drop I thought i'd be getting from my Ethylene refrigerant. Running the second stage condenser below -30C and 400 psi, no condensation was occuring, despite the fact that my Ethylene should have begun condensing around ~300 psi. After some investigation, it figured out that the Ethylene refrigerant was highly contaminated (about 30%) with Hydrogen gas from running the catalyst too hot during the production process. This resulting in the partial pressure of Ethylene being reduced to the point that condensation couldn't be achieved at a reasonable total pressure. Using a converted ice maker, i built a second cascade system where the second stage was essentially static, as opposed to a continuous loop. The purpose of this was to collect my ethylene and get it to the lowest possible temperature and condense it under pressure, then release it and hopefully allow the hydrogen to be purged out by phase separation. This allowed me to analyze the behavior of my gas mixture, and i found that at -38C, the mixture that should have condensed at around ~16 bar actually required ~23 bar to condense. This information is what allowed me to make a rough determination of the Ethylene's purity (around 70%). Unfortunately, my attempt to purify the Ethylene through phase separation simply resulted in all of it boiling off because my flow rate was so high. However, in the process, I did manage to capture a temperature drop on my thermocouple of as low as -83C, meaning Ethylene did in fact condense in my icemaker unit and then evaporate again, so while I technically achieved cascade refrigeration, there's more work that has to be done before I can get continuous refrigeration down to -100C, which will be the focus of my next video. The two main areas of improvement are: -Making Ethylene of a significantly higher purity (95% or higher) -Fine tuning the second stage flow resistance / high side volume / low side volume for optimal flow rate / pressure drop Once temperatures of -100C can be consistently achieved, it will become possible to produce Liquid Methane (or LNG), such as what's used in modern rocket engines like the SpaceX Raptor. This will be done by using a third compressor to take natural gas from a residential source and condense it at a pressure of 26 bar (370 psig) at -100C. When expanded back to 1 bar, the temperature will drop to -162C. Music: Kevin MacLeod - George Street Shuffle
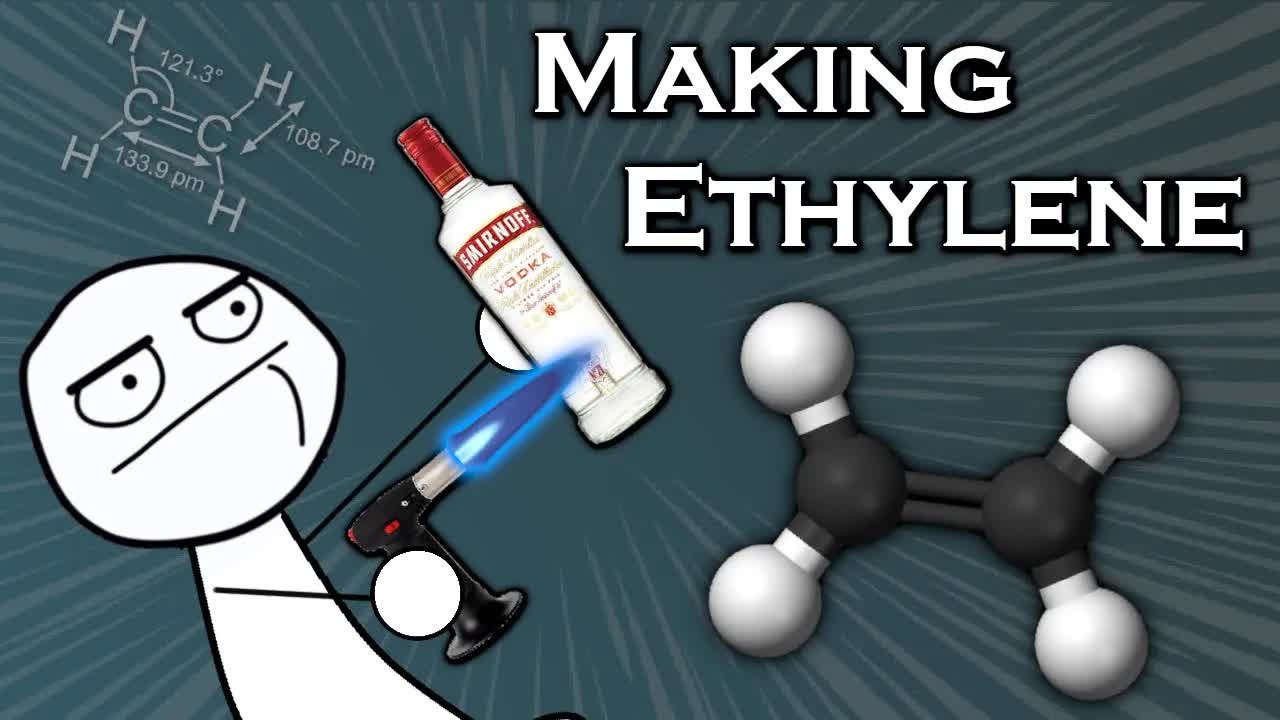
UKFEbYdKdJg | 22 Apr 2023
First off, huge thanks to Exotic Chem Lab for helping me with this video. He's provided me with the valuable information I need to create my own DIY cryocooler. He just started his youtube channel, which you can find at the link below: https://www.youtube.com/@Exotic_Chem_Lab In this video, I'll be making Ethylene (also called "Ethene", but not to be confused with "Ethane") gas to use as a refrigerant in the second stage of a two-stage vapor-compression system. Ethylene has the formula C2H4 (as opposed to Ethane, which is C2H6), and has a boiling point of -104C. However, at a pressure of about 16 bar, its boiling point rises to -37C. This means if i compress it to at least 16 bar and then cool it with the evaporator coil from my propane-based vapor compression system, i can force it to liquify, and then expand it in an evaporator to below -100C. This would technically qualify as cryogenic, at least according to US EPA specifications, which considers any temperature below -90C to be "cryogenic". Typically, a cascade refrigerator would use R508 as its second stage refrigerant, but this substance is no longer produced for environmental reasons, so it's prohibitively expensive. This makes Ethylene the only practical alternative for a hobbyist. Ethylene is also sold as "R1150" refrigerant, but difficult and expensive to acquire in this form. In some countries it may require a license to buy. Fortunately, DIY production is relatively simple. By boiling ethanol and passing the vapors over an activated alumina (Al2O3) catalyst, the ethanol molecule is dehydrated as follows: C2H6O = C2H4 (gas) + H2O (gas). The output gases are then bubbled through liquid water, and the steam condenses, leaving behind the ethylene gas. The only catch is that the dehydration has to proceed within a certain temperature range. The optimal temperature for ethylene production is about 450C +/-50C or so. Once the catalyst drops below 350-400C, the majority of the ethanol becomes diethyl ether or (C2H5)2O. Above about 500C, the ethanol molecule starts to decompose entirely, producing pure hydrogen and pure carbon. For this reason, it's necessary to use a thermocouple in the catalyst vessel to ensure optimal temperature is maintained. Ethylene has a very distinct smell that many people describe as "faintly sweet and musky". To me, the smell is very similar to rotting/overly ripe fruit. It quickly becomes nauseating and can cause dizziness depending on the concentration. A more serious hazard of this gas is that it has almost exactly the same density as air. This means if undisturbed, a cloud of highly flammable ethylene can sit in one spot instead of sinking to the floor like propane or floating up and escaping like methane or hydrogen. For storage, i collected the ethylene gas in a beach ball then used a fridge compressor to force it into a 2.5 gallon (9.5L) air tank, which had been evacuated, flushed with propane multiple times, then evacuated again to ensure no explosive mixture would occur. This will then be fed into the low-pressure side of the second stage of my vapor compression system when it's built. Music Used: Fortaleza - Topher Mohr and Alex Elena Lobby Time - Kevin MacLeod Bossa Antigua - Kevin MacLeod

7QZrHzd3RA8 | 11 Apr 2023
In this video i'll show how to put together a single-stage vapor compression refrigeration system and explain the theory behind it. This machine uses propane (R290) as a refrigerant, because it has properties very similar to standard Hydrofluorocarbon (HFC) refrigerants, but is extremely cheap and readily available, and has almost no negative environmental effects. The obvious disadvantage is its flammability. If you're careful, though, propane or butane are perfect substances for a DIY vapor compression system. This is still part of my long term project to build a DIY cryocooler to make my own liquid nitrogen, but I've pivoted away from gas-phase systems like stirling/GM and decided to focus more on phase change systems due to the greater availability and low cost of parts. In upcoming videos, i'll be staging multiple vapor compression loops together to get temperatures below -100C. After that, i'll use a joule-thompson cycle to make the final push down to liquid nitrogen temperatures, but will do so with a mixture of hydrocarbons rather than nitrogen. Here's some performance specs of the device in this video: Condenser Pressure: 10-15 bar Condenser Temperature: 27-44 C Evaporator Pressure: 1.2 bar Evaporator Temperature: -37 C Capillary tube ID: 1mm Capillary tube length: 2m Compressor nominal rating: 5,000 BTU Compressor locked rotor amps: 27A Compressor operating limit (estimated): 5.4A Input power: 667W (529W from compressor, 138W from fans) Refrigerant charge: ~50 grams of propane Maximum recorded cooling power: 116W (COP 0.173) *Note that this power was recorded by testing the temperature drop of water reservoir at room temperature with lots of heat leaks, which was a far from optimal condition. Also, recording cooling power by multiplying the water flowrate of 13.5 grams/sec by water's heat capacity times the temperature differential across the coil of 3.3C yielded a higher cooling power of 186W. In upcoming videos, this system will be used to cool the condensor of a second refrigeration circuit, which will then evaporate to a far colder temperature close to -100C. This requires ethylene as a refrigerant (R1150). It's pretty hard to find and expensive to buy commercially, so in the next video, i'll be showing how to make it. Other useful tidbits: Propane bottle NPT thread adapter: https://www.amazon.com/Hooshing-Propane-Adapter-Throwaway-Cylinder/dp/B082MBGVXN/ Condenser fan: https://www.amazon.com/BLACKHORSE-RACING-Universal-Electric-Radiator-Thermostat/dp/B07DLSPDN1/ -Window AC unit that was stripped for condenser coil was rated at 5,000 BTU. The manufacturer/model number you use is not important as long as its sized right. Music Used: Kevin MacLeod - Lobby Time

q_dVvGQ72YY | 09 Mar 2023
In this video, I'm going to show how to make dry ice (frozen CO2) from scratch. I thought using dry ice to pre-cool my pulse tube cryocooler might help me get lower temperatures, since dry ice is -79C, and adding my pulse tube's ~100C temperature drop on top of that could get me very close to liquid nitrogen temperatures. But instead of just buying dry ice, I wanted to see if it was feasible to make it myself, so I went through the steps of producing, cooling/compressing, and discharging the CO2 as liquid to form ice. There are several ways to produce CO2 - a few of these are: -Reacting acid with baking soda -Cooling and collecting exhaust from combustion of hydrocarbons -Capturing exhaust from yeast as it consumes sugar -Capturing human breath -Dissolving atmospheric CO2 in water and extracting it under vacuum -Reacting atmospheric CO2 with Calcium Hydroxide, creating Calcium Carbonate, then decomposing the Calcium Carbonate to release CO2 and Calcium Oxide. The Calcium Oxide is later regenerated back into Calcium Hydroxide with sodium hydroxide. Once the CO2 is captured, it has to be stored. In theory, large gas bags could be used, but that's not very practical, so i used a fridge compressor to force the captured gas into a compressed air tank at ~160 PSI (about 12 bar). Using a 10 gallon (38L) tank, i stored approximately 1.8 lb (0.82kg) of CO2 gas. However, to freeze CO2, it first has to be liquified by either high pressure, very low temperatues, or both. To liquify at room temperature around 25C requires about 60 bar of pressure (~867 psi), but my compressor was only capable of producing about 400 psi (about 28 bar). In order to liquify the CO2 at this pressure, i had to put the tank in an ice bath at 0C. Even this wasn't quite enough, though, so to get a little bit of extra pressure, i fed the output from the 12 bar tank into the suction side of my compressor, allowing it to produce close to 600 PSI at the discharge side. In the ice bath, this was enough pressure to liquify the CO2, but it took a little over an hour to transfer and condense the CO2 from the 12 bar tank. I collected about 500 grams of liquid CO2 in the high pressure tank. Once I had the liquid CO2, i turned my high pressure tank upside down so that the liquid would come out first, and discharged it. Liquid CO2 can't exist at 1 atmosphere of pressure, so as soon as it comes out of the tank, it flash freezes to dry ice at -79C. The tricky part is capturing the frozen CO2, since most of it blasts out into the atmosphere. The container being used to capture the ice needs to be vented to work properly, but not vented too much, or else all the CO2 will be lost. To do this, I tried a sock (effectively a porous container), which probably collected less than 20% of the CO2 from the tank as ice, and came out in a fine powder, meaning it didn't last long. The second approach used a mold with velt holes, but i only recovered about ~2% of the CO2 this way. I think the key to creating a block of dry ice is to discharge relatively slowly into a mold. I had my valve full open, and I think instead of allowing ice to collect and settle in the mold, the flow was blasting it out. Ultimately, the time and cost of producing the dry ice from scratch make it impractical as a pre-cooler for liquid nitrogen generation. Music Used: Kevin MacLeod - Lobby Time Kevin MacLeod - George Street Shuffle Kevin MacLeod - Groove Groove
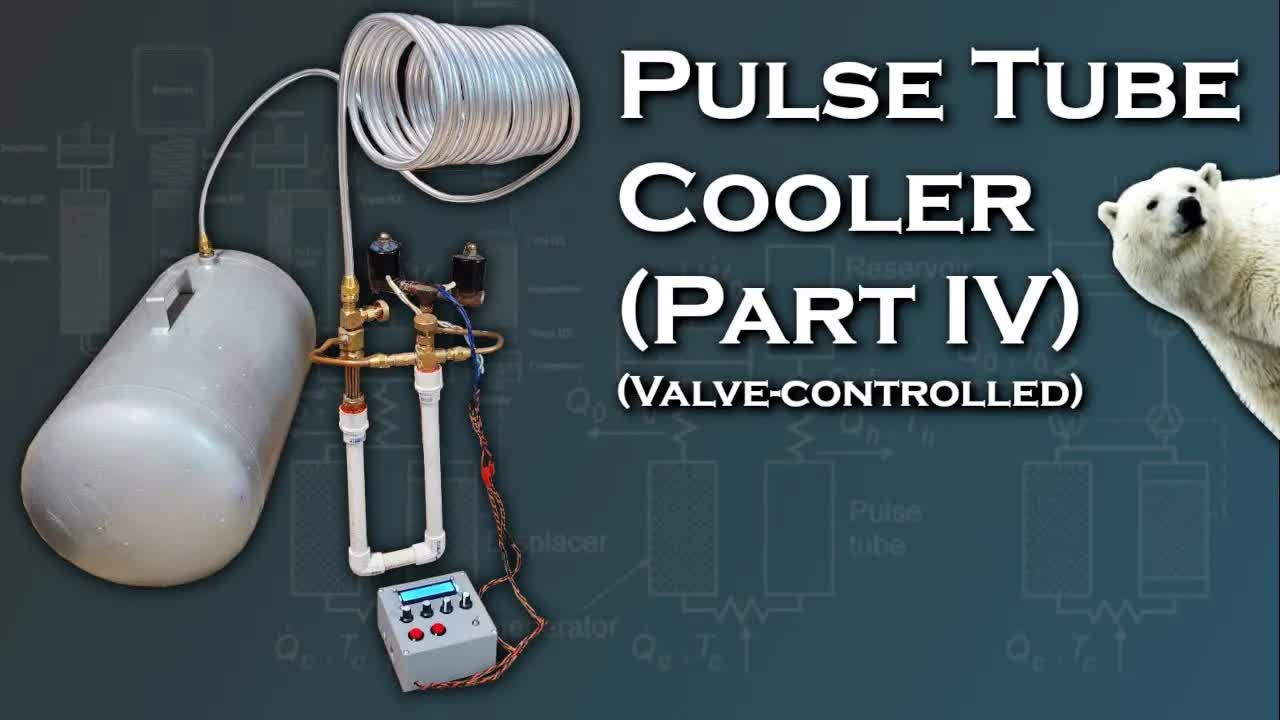
vC2it8LHKSQ | 17 Feb 2023
This is the 4th part in my video series on designing/building/testing a pulse-tube cryocooler in an attempt to create low enough temperatures to liquify nitrogen (-196C or 77K). In this video, i'll be investigating an entirely different type of pulse tube that uses two valves - one connected to a compressor and another vented to the atmosphere - to create the pressure oscillations in the pulse tube. This is known as a "Gifford-McMahon" (GM)cycle, and is more commonly used in a refrigeration cycle with a moving displacer, but can also be found in use with pulse tubes. The GM cycle is less efficient than using a piston (stirling-type) to generate pressure oscillations, but has the advantage that it's cheaper and easier to build, since it can be coupled with a variety of different compressors and matching acoustic impedance is not neccesary. GM-type cycles typically operate at a COP of under 5% of Carnot, whereas advanced stirling-type coolers can approach 30% of Carnot. Despite this, GM cycles are the primary type used in terrestrial applications, such as cryocoolers in labs and production facilities where modest quantities (under 10L per day) of LN2 are required. Despite the increased energy consumption, this configuration is typically cheaper to install/maintain than stirling cycle coolers, which are usually reserved for aerospace applications, like being mounted onboard sattelites or missiles to cool optics. For the valve assembly, i used a pair of solenoid valves activated by MOSFETs which could have their timing controlled by an arduino with a front panel display, allowing me to know the exact timing I dialed in, which was very convenient for repeatability. Real GM cycle coolers use a rotary valve connected to a motor inside the pressurized assembly, which is more reliable than solenoid valves. The entire assembly runs at around 0.5 hz. Typical commercial units range between 1-2 hz, in contrast to stirling cycle units, which can operate anywhere from 20 hz to 100 hz. However, pressure ratios are typically much higher on a GM unit, ranging from 2-3 with a baseline pressure typically from 10-30 atmospheres, whereas pressure ratios on stirling units are usually in the neighborhood of 1.1-1.3. Most GM units will have a high pressure side around 200-400 psi and a low pressure side from 50-200 psi, depending on the cold head and compressor being used. The lowest temperature i achieved running on compressed air was -83C, but I didn't consider this a valid result, because I wasn't able to repeat it. The lowest repeatable temperatures were in the low 70's, basically matching the performance of my previous stirling-type pulse tube. Considering that the power input required was close to 1 kW, compared to the previous design's power of ~120W max., it's clear that this setup is far less efficient. One of the major sources of inefficiency is the fact that my low-pressure side is simply connecting to the atmosphere, rather than being connected back to the compressor in a closed loop. This is because my current compressor isn't hermetically sealed, and not meant to operate with input pressures over 1 atm. With my high side pressure at 100 psi, theoretically, the most efficient low side pressure would be somewhere between 40-60 psi. In the next part of this series, I'll be generating hydrogen and using it as a working fluid instead of air, with a closed-loop system running off a hermetically sealed fridge compressor. This will dramatically increase internal heat transfer, making the whole system more powerful and efficient, and should bring me much closer to my goal of -196C. Part I: https://www.youtube.com/watch?v=GjRoThMyNGA Part II: https://www.youtube.com/watch?v=WOmjJFk8rl0 Part III: https://www.youtube.com/watch?v=cy8aGMH8Tz4 Music Used: Kevin MacLeod - Lobby Time Kevin MacLeod - George Street Shuffle

cy8aGMH8Tz4 | 21 Jan 2023
This is the third video in my series on building/testing a Pulse Tube cryocooler with the eventual goal of liquifying nitrogen/oxygen. Part I: https://www.youtube.com/watch?v=GjRoThMyNGA Part II: https://www.youtube.com/watch?v=WOmjJFk8rl0 In this video I investigated the effects of different pulse tube materials, regenerator materials, heat sink designs, inertance tube geometry, and pressurization of the working fluid. While I didn't manage to exceed my record from the previous video of -75C drop (corresponding to a drop below ambient of about 100C), I did gather a lot of information about design factors. My initial design in this video used a stainless steel pulse tube/regenerator housing, but i found that the temperature difference generated for a given power input was dramatically lower than with PVC parts due to conduction losses. One of the biggest takeaways from the tests i ran was that performance is almost directly proportional to the pressurization of the working fluid, and having a large average pressure is much more important than having a high compression ratio. This is consistent with how real cryocoolers are built, which are typically pressurized anywhere from 10 to 30 atmospheres, but have pressure oscillations of under 10% of average pressure. I also experimented with different regenerator materials, such as ceramic beads, glass beads, plastic pellets, and glass fibers, but found that compacted stainless steel wool (which i started with) still performed best. For configurations both with the 25mm diameter piston and the 40mm diameter, i found that the cooler seemed to hit a wall at around ~100 degrees of temperature drop below ambient, where application of additional power only marginally improved performance. I suspected this was related to limitations imposed by the inertance tube and compared my 1/4" copper tubing against 3/8" flexible silicone tubing of a greater length, but I found that this change reduced performance, most likely due to increased surface roughness and flexibility in the line dissipating energy. In a future video I'll probably try to use rigid copper/aluminum tubing with a 3/8" or 1/2" inner diameter. I also reconfigured the entire device into an alpha-type stirling cooler, but found that performance was actually dramatically reduced despite the ability to mechanically set the phase angle between compression and expansion. I think this is because the cold expander piston was causing large conduction losses through its thin aluminum walls. I ran the device with loads disconnected, and with pistons disconnected to determine the amount of power being consumed by mechanical action as opposed to pneumatic power, and found that less than 30% of the input electrical power was actually going into the system. Finally, I examined the effect of a double-inlet valve, which has the effect of improving phase shift and removing some of the load on the regenerator. While this didn't make a tremendous difference, the difference is very obviously apparent and repeatable. In my next video, I'm going to build an entirely different test setup using a valve-based (or "Gifford-McMahon") configuration and a standard air compressor as a high pressure source. While this configuration is less efficient, because the input power would be so much larger, it should be an overall net positive. In addition, control over valves allows me to achieve consistent timing via digital control and fine tune it for best performance.

WOmjJFk8rl0 | 27 Dec 2022
Part 1: https://www.youtube.com/watch?v=GjRoThMyNGA This is the second part of my video series on attempting to build a Pulse Tube cryocooler. I managed to make significant progress by removing the linear motor and using a conventional rotary motor with a large gear reduction ratio and a flywheel to produce the larger forces needed for higher compression ratios. For pistons, I used pneumatic actuators. I evaluated a 25mm bore and a 40mm bore piston, both with a 50mm stroke. Pneumatic actuators have more friction than conventional pistons due to their rubber lip seals, but theoretically have zero blowby, so they hold pressure, which makes them more effective for low frequency applications. Here are some specifications for the cooler: Pipe diameter: 18mm Regenerator Length: 30mm Regenerator Material: Fine steel wool Pulse Tube Length: 100mm Flow resistance source: 1/8 NPT needle valve Inertance Tube Length: 10' (~3m) Inertance Tube Diameter: 4.4mm Buffer Tank Volume: 2L Piston Swept volume (25mm): 23CC Piston Swept volume (40mm): 57CC Compression Ratio (25mm): 1.4 Compression Ratio (40mm): 2.0 Maximum Frequency: 15 Hz Motor KV: 750 Motor Voltage: 16V Motor reduction ratio: 5:1 Flywheel moment of Inertia: 0.012 kgm^2 Maximum recorded temperature drop below ambient: -91C Lowest recorded temperature: -75C I think with some more optimization, this system can probably reach -100C, although without helium or hydrogen as a working fluid, I think it's unlikely that I'll reach cold enough temperatures to liquefy oxygen/nitrogen. In part 3 of this video, I'll do more investigation into hot-end heat exchanger design, regenerator design, and the effect of increasing the power density of the system by pressurizing it. I'll also be comparing the pulse tube performance to a similar spec alpha stirling cooler. Links for parts: Motor: https://www.amazon.com/dp/B084QCLTM1?psc=1&ref=ppx_yo2ov_dt_b_product_details 25: and 40mm pistons: https://www.amazon.com/gp/product/B082FW5XKS/ref=ppx_yo_dt_b_search_asin_title?ie=UTF8&th=1 https://www.amazon.com/dp/B08YYQZ5CQ?ref=ppx_yo2ov_dt_b_product_details&th=1 Music Used: Kevin MacLeod - Lobby Time Kevin MacLeod - Groove Groove

GjRoThMyNGA | 07 Dec 2022
In this video i expand on the resonant linear motor from my previous video and use it to drive a linear compressor for a pulse-tube refrigerator. A pulse tube refrigerator is used to reach cryogenic temperatures, with some going into the sub-kelvin temperature range. These are typically used in labs for scientific experiments that require extreme low temperatures, or for sensors on sattelites/spacecraft, like the optics on the James Webb Space Telescope. From a thermodynamic standpoint, a pulse tube cryocooler is effectively the same as a Stirling or Gifford-McMahon (GM) cooling cycle, but it replaces the displacer (or expander piston in the case of an alpha-stirling) with a gas piston. With careful tuning of a needle valve, inertance tube (gas momentum tube), and buffer volume, the phase of the gas piston's motion is shifted from the pressure oscillations of the compressor (by ~60-90 degrees), allowing heat pumping to occur out of the cold end. The major advantage of this device is that it eliminates moving parts from the cold end, which would be the displacer piston in the case of a Stirling or GM cooling cycle. While i did manage to create a working linear compressor with a tuned dynamic balancer to create pressure oscillations, the linear motor didn't seem to have enough force to create a reasonably large compression ratio, and i only managed to produce a minor temperature difference. However, actuating the piston by hand, i was able to produce a temperature drop of around 4C. Pulse tubes are also extremely dependent on the tuning of the needle valve, inertance tube, and buffer volume, which act like an electrical RLC circuit to create a specific phase shift at a specific frequency. The pneumatic tuning in this video was far from optimal. In the next part of this series, i'll be replacing the linear compressor with a rotary compressor that I plan to build with an air cylinder driven by a geared down brushless motor from an RC plane. I'll also be focusing heavily on tuning the inertance tube / buffer volume, and optimizing heat exchangers to remove energy from the system even at small temperature differentials. Previous video on building a linear motor: https://www.youtube.com/watch?v=u7k2wiY4Flo&t=11s If you want to understand the basics of different cryocooler types, these articles are helpful: https://www2.jpl.nasa.gov/adv_tech/coolers/Cool_ppr/CEC2005%2050yr%20History%20of%20Cryo%20in%20Space.pdf https://www2.jpl.nasa.gov/adv_tech/coolers/Cool_ppr/Chap%206-Refrig%20Sys%20for%20Achiev%20Cryo%20Temps_2016.pdf This is a helpful overview of how different pulse tube configurations work: http://large.stanford.edu/courses/2007/ph210/bert2/ This paper explains more about the math in computing resistance/inertance/compliance and phase shift: https://trc.nist.gov/cryogenics/Papers/Pulse_Tube_Cryocoolers/2006-Inertance_Tube_Optimization.pdf Another resource i found tremendously useful was https://cryocooler.org/. Under "Past Proceedings - Volumes 14 to 20" you can select a volume and under "Table of Contents" there's dozens of research papers on Stirling/GM/Pulse Tube cryocooler development. STL Files (these are for the linear compressor with the TPU bellows piston): https://www.thingiverse.com/thing:5684574 Music Used: Heatley Bros - Sunset Beach Kevin MacLeod - George Street Shuffle Kevin MacLeod - Lobby Time
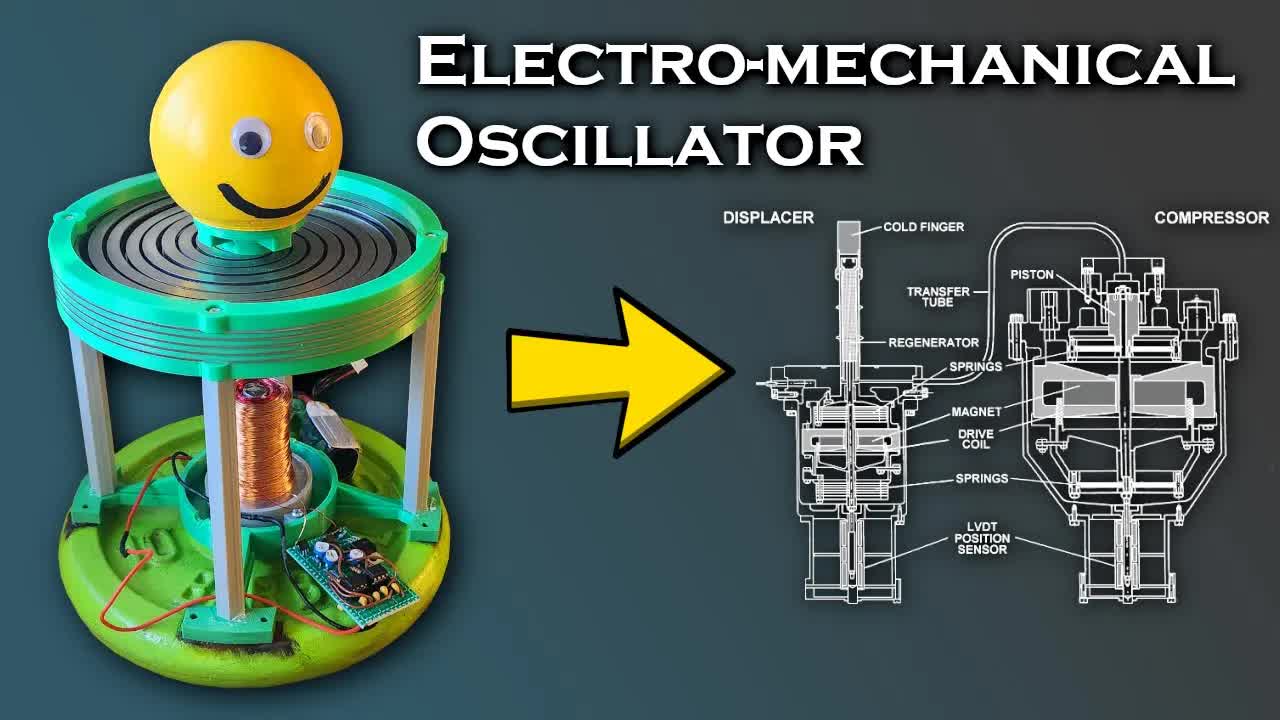
u7k2wiY4Flo | 30 Oct 2022
In this video I'll show how to build a resonant mechanical oscillator that's driven by an electromagnet. The electromagnet is pulsed by a circuit with an adjustable frequency, so it can be fine tuned to run at the exact resonant frequency of the spring-mass system. In this case that frequency is about 11 Hz. The driver basically just consists of a 555 timer and a MOSFET to turn the coil on and off. In the future, i think i need to use a feedback controller to do this, because even when i get the system to resonate, it eventually drifts out of phase and resonance dies off (even though the frequency is matched). This type of device is commonly found in the compressor section of compact cryocoolers for infrared imaging and other sensors that require extremely cold temperatures to operate. Suspending the compressor pistons on a flat spring or "flex bearing" and driving them at resonance allows for high power and efficiency even with the relatively weak forces between the magnets and the coils. This is analogous to a flywheel on a crankshaft, but is lighter, smaller, and more reliable. By avoiding the need for the bearings and linkages present in a rotary system, this kind of devbice can achieve an extremely long service life (some are rated for over 200,000 hours of operation) inside a hermetically sealed unit. This is part of my investigation into building my own refrigeration system (and eventually cryocooler) without HFC's/phase change refrigerants. Several months ago i made a video showing how i built a compressed air turbine which I intended to use as a Brayton cycle cooler, and while it did work, the extremely loud noise made it impractical in a home environment, so I'm now investigating reciprocating systems like Stirling/Pulse Tube/Thermoacoustic/Gifford-McMahon-type devices for generating extremely low temperatures. Music Used: Kevin MacLeod - George Street Shuffle Kevin MacLeod - Groove Groove (Yes, this is the same song that's in Kerbal Space Program) STL Files: https://www.thingiverse.com/thing:5594081 Metal Spring DXF file: https://drive.google.com/file/d/1OX4CL7d9jAzPwvoHF9XoKwuRwrusV23V/view?usp=share_link Driver circuit schematic: https://drive.google.com/file/d/1chrHYzkV6LTJ1hQsXgQ6WjCTgmVXKFEx/view?usp=share_link Further reading on cryocoolers: https://www2.jpl.nasa.gov/adv_tech/coolers/Cool_ppr/CEC2005%2050yr%20History%20of%20Cryo%20in%20Space.pdf https://www2.jpl.nasa.gov/adv_tech/coolers/Cool_ppr/Chap%206-Refrig%20Sys%20for%20Achiev%20Cryo%20Temps_2016.pdf Fabrication shop i used for the metal springs: https://sendcutsend.com/

2Vb82SZE3JA | 07 Oct 2022
In this video I'll show the technique of "Kirlian Photography", which uses corona discharge off a conductive object for imaging. The technique uses two clear glass plates with salt water between them. The salt water is connected to a high voltage, high frequency AC source. An AC flyback transformer works for this, but i got better results using a solid state tesla coil operating off a slayer exciter circuit - the same circuit i demonstrated in my previous video. This generates around 40,000 volts at 350 kHz with a 12V input. The high voltage AC doesn't conduct through the glass, but causes high voltage charges to appear on the outside surface of the glass plates through capacitave coupling. Because glass is an electrical insulator, the charges can't move freely along the surface, so when an electrode connected to ground comes near the glass, the resulting discharge "fans" out, as charges from a relatively large area will jump to a single point electrode. When a flat conductive object is pressed against the glass, the edges and small bumps on its surface will exhibit this type of discharge and glow purple. Since the glass plates and the saltwater are transparent, the resulting glow can easily be photographed. This results in some extremely interesting and visually impressive effects, but is mostly limited to flat conductive objects like coins, keys, blades, etc. I've seen some videos that use acrylic insulators for doing this - which I strongly advise against, because the discharges will heat up and melt the acrylic - leaving a permanent mark or even burning a hole through the sheet. Also, if you want to do this project and you're building an AC flyback, be mindful of the secondary coil inductance and its resonant frequency. I found that by having an enormous turns ratio at a high frequency, the transformer operating frequency was actually well above the resonant frequency between the coil and any parasitic capacitance - which causes tremendous losses and erratic performance - this problem is avoided with the solid state tesla coil. Music Used: Serge Pavkin - To the Stars Serge Pavkin - Atmospheric Ambient Serge Pavkin - Andromeda Serge Pavkin - Cosmic Glow

xImmwL5MR0o | 17 Sep 2022
In this video I'll show how i built a battery powered solid state tesla coil that fits on a desk or a coffee table. The coil uses a "slayer exciter" circuit with an RC snubber and reverse protection diode to avoid damaging spikes of voltage/current during "hard switching". In addition, 3 FETs are used in parallel to spread out the heat load, which makes the circuit far more reliable. In addition to those changes, I've buffered the MOSFET gate drive with a push-pull pair consisting of an NPN and PNP transistor. This allows the gate to be turned on and off much faster, and allows more control over the gate voltage by using a resistor divider on the base of the transistor(s). The circuit is interrupted with a 555 timer. It runs at approximately 60 hz and 30% duty cycle. This gives the arcs a more sharp/jagged shape, but also reduces the power consumption and heat load. Another useful feature in this driver is the low voltage cutoff circuit, which shuts off the gate drive transistors if the supply voltage falls below 22V. This ensures that the lithium battery won't be over-discharged. The maximum arc length i've observed on this coil is approximately 4" (10 cm), which is very impressive considering that the supply voltage is only 24V. You may have also noticed that I used a sharp electrode for a breakout but no toroidal / spherical top load. This is to reduce A few specs: Primary Turns: 2 Secondary Turns: ~1200 Secondary Diameter: 3.5" Secondary Height: 6.0" Input Voltage: 24V (Nominal) Current Consumption: ~4A Operating Frequency: ~300 kHz Interrupter Frequency: ~60 Hz Duty Cycle: 30% Snubber R/C: 2 Ohm / 54 nF Parts I used: IRF640 (3 in parallel for driving the primary) 2N3904 / 2N3906 (gate drive transistors) 2N3904 for undervoltage cutoff / interrupter pull down MUR120G (Rail diodes) NE555 (Interrupter) LM833 (Undervoltage cutoff comparator) Music Used: Kevin MacLeod - George Street Shuffle Kevin MacLeod - Lobby Time Serge Pavkin - Crystals

ooPlDbRXzAc | 04 Sep 2022
In this video I'll show how i use a diode-capacitor chain to boost 9,000 volts AC to over 500,000 volts DC. This is known as a "Cockroft-Walton" type generator, and was used to generate high energy discharges for early particle accelerators. It looks very similar to a Tesla coil, but it's sort of the exact opposite, because it outputs DC instead of AC. This gives it a unique capability that a Tesla coil doesn't have - it can produce static electricity. In fact, at 500kV, some objects can be given enough static charge to repel each other like magnets. It'll pull your hair toward it from across the room - similar to a Van de Graaf generator, but much more powerful. The input to the multiplier is 9,000 volts peak at around 50 kHz from a flyback transformer i wound myself being driven by a ZVS driver with a 24-volt supply from a 6S LiPo battery. I've covered the ZVS driver in several of my other videos, so I didn't bother to do so in this one. If you're thinking of recreating this project, just keep in mind that a discharge from this device is far more dangerous than an arc from a Tesla coil. The current from a Tesla coil will travel along the outer surface of your skin because of the high frequency AC - usually in the hundreds of kHz. The DC discharge from this multiplier will go straight through your body. Always make sure to use a long, non-conductive (DO NOT use wood!!) stick with a solid connection to ground when you're making arcs, and when you're finished, keep the electrodes shorted together for a minute or so to ensure any residual charge has bled off. Capacitors and diodes are just cheap units off of amazon: 20 kV / 100 mA diodes: https://www.amazon.com/2CL2FM-100mA-Voltage-Diode-Rectifier/dp/B074S8JT96/ 20 kV / 1 nF capacitors https://www.amazon.com/dp/B07V3XMHHL Music Used: Kevin MacLeod - Lobby Time Kevin MacLeod - Hard Boiled Kevin MacLeod - Groove Groove
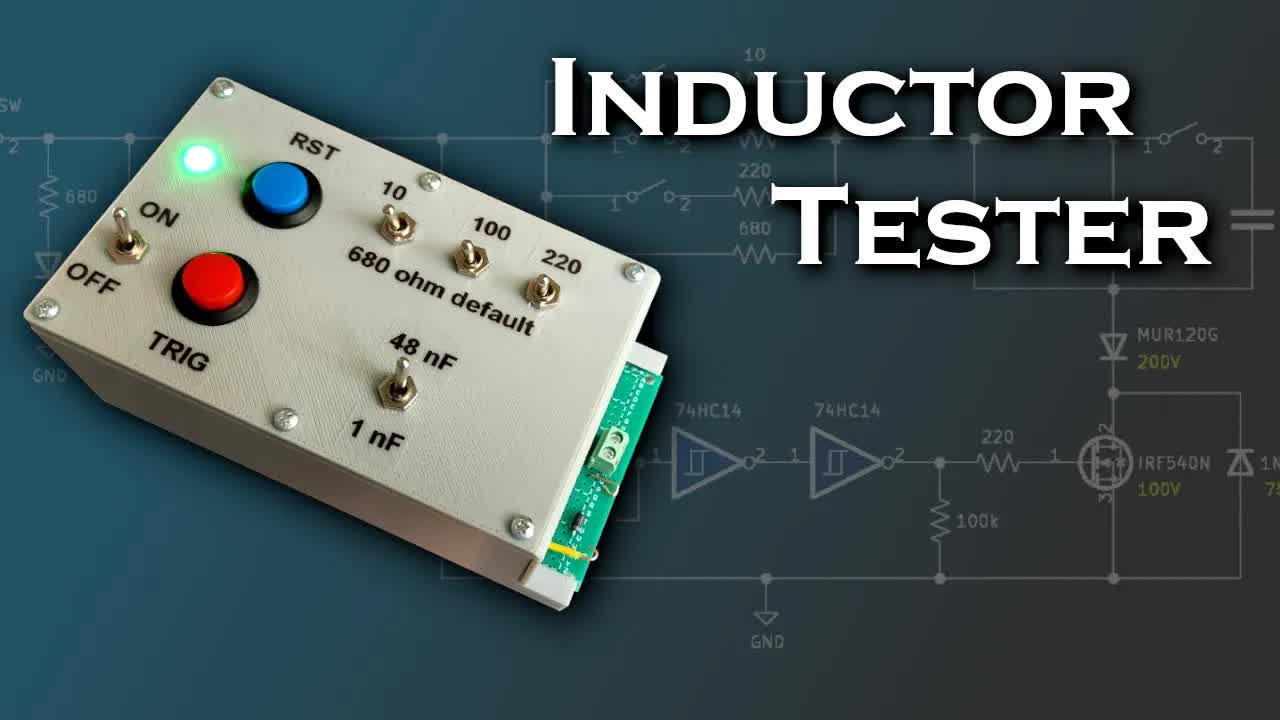
IRRF1FadkFw | 05 Aug 2022
In this video i show how to build a circuit that can measure the value of an inductor in conjunction with an oscilloscope. This is meant to be a replacement for my $10 LCR meter, which isn't very accurate, and has very poor resolution below ~1mH of inductance. The circuit works by sending a single pulse through an inductor, which has a known capacitance in parallel with it. When current through the inductor is shut off, the L-C pair "rings" at its resonant frequency, determined by f = 1/[2pi*sqrt(LC)]. Since frequency "F" and capacitance "C" are known, the inductance can be determined. Current through the inductor under test is limited by current limiting resistor(s), which are manually configured by toggle switches. By default, a 680 ohm resistor is connected in series with the inductor, but 220, 100, and 10 ohm resistors can be toggled as well to allow more current for the test pulse. This is because smaller inductor values need to be pulsed with a larger current to generate a readable "ringing" signal, due to their lower energy storage for a given current. In addition to multiple resistor options, there are two capacitance values that can be tested against. By default, a 1 nF capacitor is connected in parallel with the inductor under test, but a 47 nF can be added in parallel by toggling a switch. If you don't have an oscilloscope, it may also be possible to measure frequency using a high impedance AC coupling to a schmitt trigger which would send square wave pulses to an arduino or similar microcontroller to be measured. This is a valuable addition to any power electronics toolkit, because inductors/chokes and transformers are used so often, and knowing the exact component values is crucial for design optimization. However, if you're only looking for something to give you a rough approximation of inductance / capacitance, the cheap amazon/ebay LCR meters will still get the job done, and I've used this one for several years: https://www.amazon.com/AITRIP-Transistor-Capacitance-Capacitors-Thyristors/dp/B091356Q9T/ Automatic coil winder video: https://www.youtube.com/watch?v=GJcQfJ6JTZg&t=419s Music Used: Lakey Inspired - Chill Day Lukrembo - This is for you Kevin MacLeod - Lobby Time
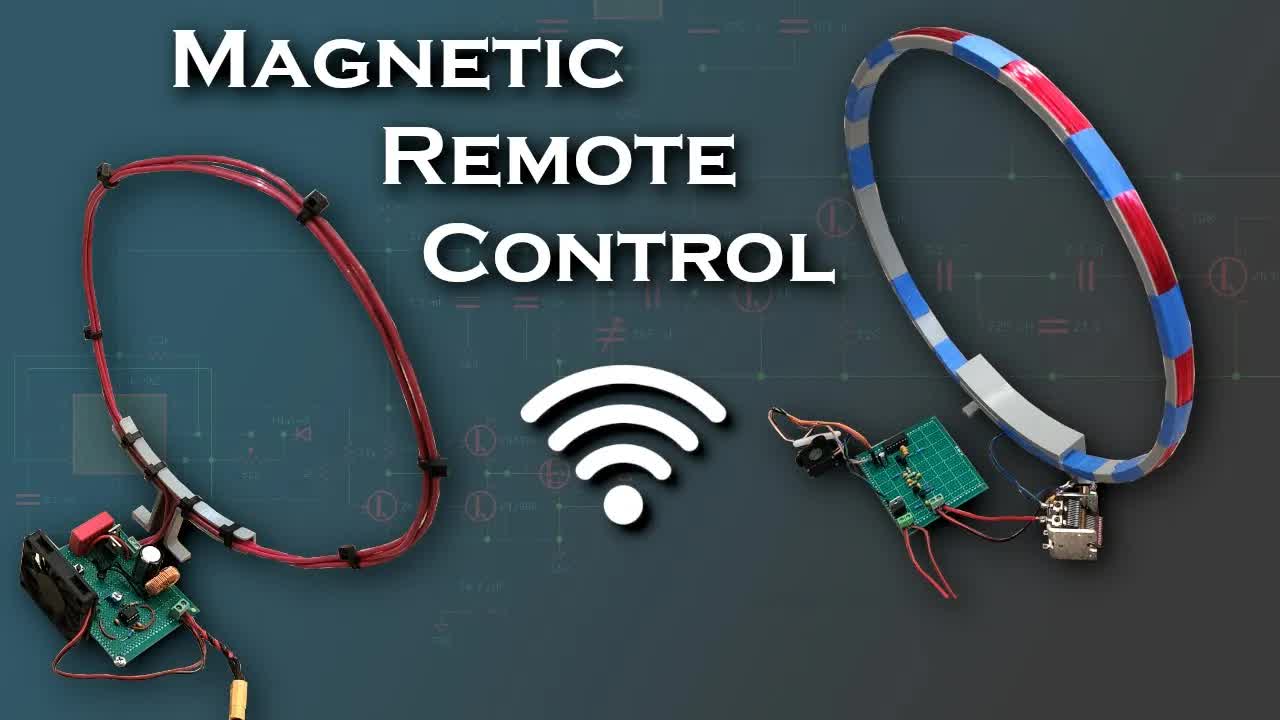
AvyeK_MXTL0 | 09 Jul 2022
In this video I'll show how I built a remote control that works entirely off the magnetic field of a coil (unlike a typical radio transmitter). This is known as inductive coupling, an is the same principle used in a transformer. The only difference in this case is that the windings of the transformer are very far apart. This type of signaling is common in short-range, low power devices, like RFID. This is effectively the same setup that would be used for wireless power transfer, but with two key differences: -The output of the transmitting coil is not a continuous wave; it's modulated to produce a signal -The signal of the reciever coil is amplified (by about +70 dB) The transmitter produces a series of damped oscillations at 69 kHz, with a pulse frequency that can be varied between 1.3 kHz and 2.3 kHz. The reciever circuit the same design as you'd find in a simple AM radio, the only difference being that the frequency used here (69 kHz) is far below the AM band. The reciever extracts the signal tone, and cleans it up through a schmitt trigger to produce a 0-5V square wave. The schmitt trigger output is sent to an Arduino Uno, which reads the tone frequency, and controls a standard R/C toy servo accordingly. The main advantage of this kind of transmitter is that it can be made to work without the huge antennas or elaborate grounding schemes needed to operate a typical ULF/VLF radio. The disadvantages are that it's very directional (on both the transmitter and reciever end), and the signal amplitude drops off exponentially faster than a typical radio. With an ideal omnidirectional radio transmission, the amplitude drops off with the square of the distance, whereas with inductive coupling, the drop off is approximately the 3.5th power of distance. Relevant components in these circuits: -IRLZ44 MOSFET -NE555 Timer -2N3904 and 2N3906 NPN and PNP BJT's -1N4148 Diodes -LM7805 for 5V Regulation -15 to 365 pF Variable Capacitor for Reciever Tuning https://www.amazon.com/Capacitor-Variable-Single-365-Rotation/dp/B00EQI9K9O/ Music Used: Kevin MacLeod - Groove Groove Kevin MacLeod - George Street Shuffle Heatley Bros. - Otherworld Lukrembo - This is for you

SdJwY4Huukc | 25 Jun 2022
STL Files: https://www.thingiverse.com/thing:5418100 In this video I'll show how i built an RC airboat for racing. The boat can travel on water, tile floor, and wet grass. It's powered by a 3S LiPo Battery (12V) turning a pair of counter-rotating brushlesss motors with 6" 3-bladed propellers. It's also equipped with a pump draw water from beneath the hull and shoot it out a nozzle at the front of the boat to knock over other racers. I originally equipped the boat with an audio amplifier to play music as a gimmick, but i found that it added unneccesary weight and complexity, and couldn't be heard over the sound of the propellers, so I removed it. The Hull is made from 3d printed sections that are glued together and smoothed out with body filler and epoxy resin. I hand-painted the parts instead of spray painting because I had a large supply of acrylic paints for arts and crafts. Specifications (to the best of my knowledge): Battery: 3S / 2200 mAh Motors: 1400 kV ESCs: 30A Propeller: 6" / 3 blade / Pitch Unknown Max. Current Draw: 22A Water Cannon: 80 PSI / 4LPM / 4mm Nozzle Here's the links to the part/ 4s I used if you want to build this or a similar craft: Motors & ESC Combo: https://www.amazon.com/gp/product/B00PXVG7VM/ Battery: https://www.amazon.com/gp/product/B08H7RGZB6/ Radio Transmitter/Reciever: https://www.amazon.com/dp/B0744DPPL8 Water Cannon Pump: https://www.amazon.com/dp/B01N75ZIXF Music Used: Lukrembo - This is for You Kevin MacLeod - Lobby Time Lakey Inspired - Chill Day Kevin MacLeod - Hard Boiled

shNaC7d4CMA | 07 Jun 2022
This is the first video in my series on converting a kayak into a wet submarine. I found that my original submarine was a hassle to operate, because it required a heavy trailer and had to be launched from a boat ramp. This made it difficult to accomplish my goal of diving on coral reefs in the ocean, because most boat ramps are usually several miles from inlets, and inlet crossings were hazardous in the large, slow submarine. On the other hand, this specially modified kayak is lightweight and portable. I can load it in the back of my truck, and drag it across a beach, or even through the jungle to reach springs farther inland in Florida. It will function as an ordinary kayak on the surface - being propelled either by rowing or with a trolling motor, and then submerge. Ideally, it'll be neutrally bouyant when submerged, and control its depth with dive planes. Flexible ballast bags and a powerful bilge pump will be used to return to the surface. Original Submarine: https://www.youtube.com/watch?v=GUOHjON9RVg&t=687s Arduino Code for Throttle Control: https://drive.google.com/file/d/16FM2rn-7kcdCzos7gkxweNwvR65CfFEg/view?usp=sharing Additional Info: Original Kayak: Pelican Trailblazer 100 NXT Material: "RAM-X", which is a variant of HDPE plastic Motor: Newport 36 lb saltwater trolling motor Battery Voltage: 12V Battery Capacity: 50 AH ESC: Hobbywing WP1080 ESC Control: Arduino Uno Air Capacity: 120 cubic ft @ 4,000 psi Music: Kevin MacLeod - George Street Shuffle Kevin MacLeod - Groove Groove Prod Riddiman - Lost Time Heatley Bros. - Otherworld Heatley Bros. - 8 Bit Chillout

RMUHxo2TOUk | 27 Apr 2022
NOTE: There's an error in the graphs where i label 20.1W as the max power on a data point below 20W. This was because i accidently clipped the Y-axis at 20W, but the maximum power was in fact 20.1W This is the second part of my video on building a 3d printed compressed air turbine, which you can find here: https://www.youtube.com/watch?v=Yg5swK_AnbU In this video I'll be experimenting to find the best rotor and casing geometry for a 2D-flow turbine. I'm focusing on 2D flow because of the relative ease of machining parts, since I eventually plan to build one of these out of aluminum or brass to power with steam. All the tests are conducted at 50 PSI with a 1/16" nozzle. Another goal of this project is to see if it's feasible to use a 3d-printed turbine for Brayton cycle refrigeration (like the ACM on an airliner does). This requires extracting energy from the compressed air in the form of mechanical work to drop its temperature, so a more efficient turbine will have more cooling power (and provide more mechanical output to drive auxiliary devices like a secondary compressor). Overall, my best configuration achieved a ~20% improvement over my last video, but there's a relatively large amount of scatter in my data, probably due to vibration and temperature dependance. Some further improvements I still haven't looked at are: -Tighter tolerances between the turbine rotor and casing -A convergent/divergent nozzle to convert more of the pressure energy to kinetic energy -Better seals to prevent pressure leakage between stages (or to the outside). Music Used: Kevin MacLeod - Groove Groove

Yg5swK_AnbU | 09 Apr 2022
In this video I'll experiment with some designs for a 3d printed compressed air turbine. I started this project because I wanted to research better designs for steam turbines without spending the time and money required to CNC the parts out of metal, and i got results that were almost good enough to be usable for a light duty shop tool. The highest power i measured with a simple 2D turbine on 50 PSI was 16.4 watts. I did all my power measurements with a magnetic dyno. I also built an aftercooler to remove some moisture out of the air, because I eventually want to use a compressed air turbine for the expansion phase of a brayton refrigeration cycle for cryogenic cooling (if i can get the turbine efficient enough). Both turbine designs i tried in the video use a 1/16" diameter nozzle insert that's CNC'ed out of aluminum. The results at the end of the video are both shown at 50 PSI. STL Files: https://www.thingiverse.com/thing:5347515 Music: Kevin MacLeod - Groove Groove Eric Skiff - Underclocked Kevin MacLeod - George Street Shuffle

SwzpX-jgbYM | 25 Mar 2022
In this video I'll show the upgrades I made to the CNC mill i built in my previous video: https://www.youtube.com/watch?v=R29G3hUiZnU&t=60s I upgraded to a 500W spindle and built an all-aluminum head assembly, widened the bed, increased the rigidity of the X axis with thicker rails, installed higher torque steppers on X and Z, and dramatically reduced backlash on all axes by using a double-nut arrangement on my leadscrew carriages. The machine is still far from perfect, but cutting aluminum is significantly easier now, and with some adjustments / tightening down / tuning, I think it will be able to reliably hold tolerances that are at least good enough for one-off hobby projects. Currently the most obvious weakness is flexibility in the Y axis due to using only 8mm rails. The board firmware is unchanged from the previous video. I'm still using an arduino Uno with GRBL firmware driving A4988 stepper controllers. Some links to relevant hardware: 500W Spindle kit: https://www.amazon.com/gp/product/B01LNBOCDA/ 92 oz-in Stepper Motors: https://www.amazon.com/gp/product/B00PNEQUZ2/ 16x500 mm Linear Motion Shafts: https://www.amazon.com/gp/product/B07ZK8Z2HS/ 16mm Bore Linear Bearing Blocks: https://www.amazon.com/gp/product/B07GQVBYYG/ Linear rail for Z axis: https://www.amazon.com/gp/product/B086QKJ87B/ 500mm T8x8 Leadscrew: https://www.amazon.com/gp/product/B08JPMH4V9/ 150x70x9.5 Heatsink: https://www.amazon.com/gp/product/B08T8837ZH/ Software used for CNC: Universal Gcode sender FreeCAD 0.18 STL Files: https://www.thingiverse.com/thing:5329372 Feeds/Speeds RPM: 12,000 Bit: 1/8" 2 Flute End Mill Horizontal Feed: Between 500 - 1500 mm/min Vertical Feed: 10 mm/min Stepdown/Cut Depth = 0.05mm Finishing Cut Depth = 0.01mm I found that for the same amount of volumetric removal rate, a higher horizontal speed with a smaller depth of cut gave better results because of reduced chatter/vibration. For example, 1500 mm/min at 0.05mm depth of cut was much smoother and had less chatter than 750 mm/min at 0.10 mm depth of cut. Unfortunately this does put all the work on the very tip of the end mill, but because this machine is pretty limited on power/rigidity, that's the only viable way to cut. Music Used: Eric Skiff - Underclocked Kevin MacLeod - Groove Groove Heatley Bros. - Luminare Serge Pavkin - Elevation

R29G3hUiZnU | 27 Feb 2022
In this video I'm going to show how I built a basic CNC mill. Most of the hardware was sourced from spare / leftover parts I had laying around from other projects and ended up costing me under $100. It has a working area of approximately 250mm x 250mm x 70mm and is capable of milling aluminum (though somewhat rough). The axes are moved with small NEMA17 stepper motors running at 24V, driven by A4988 drivers. The brain of the machine is an Arduino Uno running GRBL firmware, and G-code is sent to it via. USB from a laptop running Universal Gcode Sender - so everything is open source. I have a little bit of experience operating a CNC mill, but this is the first one i've built / owned. The biggest learning experience from this build was that everything needs to be tightened up and made as rigid as possible to get good results. Between leadscrew backlash and rails flexing, the spindle could easily be moved +/- 1mm or more, which causes tons of vibration, chattering, rough cutting, and loss of precision. In a future video I'll be upgrading the spindle and beefing up the structure to use 16mm rails instead of 8mm for better rigidity. I don't recommend trying to build this design yourself, because I created the printed brackets based on parts i had on hand, not what was "optimal". However, if you really want to, the STL's can be found here: https://www.thingiverse.com/thing:5262097 Music Used: Kevin MacLeod - George Street Shuffle Serge Pavkin - Atmospheric Ambient Kevin MacLeod - Groove Groove Eric Skiff - Underclocked Serge Pavkin - Fractal

1QK6zRQ8D4A | 12 Feb 2022
In this video I'll show how i used a NEMA17 stepper motor as a hand-cranked generator to charge a supercapacitor bank, which can then be used to power all sorts of things like lights, radios, or even start a fire for a survival situation. I found that using a stepper motor as a generator was far more effective than trying to build my own with magnets and coils. With a 3:1 overdrive on this small NEMA17 motor, I could easily generate 15-20V open circuit, or sustain around 2 watts of output without much trouble. The generator uses a pair of parallel bridge rectifiers (one for each coil set on the stepper) to charge a supercapacitor bank to 5.4V. It takes about 130-150 turns to fully charge a 16.5F capacitor bank, which can be done in under one minute, and keep the main light on for close to 10 minutes. To protect the capacitors against overcharging, i built a circuit using an op-amp comparator to turn on a MOSFET when the capacitor voltage goes above 5.3V and short the capacitors to prevent overvoltage. I found this to be a more effective solution than simply using a zener diode. Notable Hardware: -NEMA17 Stepper motor. Exact model doesn't really matter (i found mine in a junk drawer). -GT2 belt & Pulley, 60T and 20T: https://www.amazon.com/Zeberoxyz-Synchronous-Aluminum-Timing-20-60T-8B-6/dp/B08QZ4365D -470F / 2.7V Supercaps are Illinois Capacitor model# DGH477Q2R7 -3.3F / 2.7V Supercaps: https://www.amazon.com/MCIGICM-Capacitor-capacitance-tachograph-Electromechanical/dp/B07BLQGRQY/ -Bridge rectifiers were GBU808 harvested from random scrap devices. Really any bridge rectifier should work for this application, though. STL Files: https://www.thingiverse.com/thing:5241682 Music Used: Kevin MacLeod - George Street Shuffle

XdVXrno-3B4 | 29 Jan 2022
Update (4/29/2023) - below is a link to the STL files for recreating this project: https://www.thingiverse.com/thing:5998400/files In this video I'll show how i made a powered gyroscope that can travel along a monorail or tightrope. I'll explain how angular momentum keeps the gyro upright, even when gravity or other external forces try to knock it over. The gyro uses an 8" diameter flywheel printed with PLA, with 21 1/2" steel bolts around the edge to dramatically increase the moment of inertia. Some performance figures: Motor KV: 620 Motor Voltage: ~15V Motor Speed: ~9,000 RPM Flywheel Speed: ~3,000 RPM Flywheel moment of inertia: 0.0138 kg*m^2 Flywheel kinetic energy: 680 J Flywheel angular momentum: 4.3 kg-m^2/sec Drive motor speed: ~120 RPM The drive motor has plenty of torque to climb a steep incline, but traction is a major limiting factor, so the best i could manage was 10-15 degrees on a tightrope. In the future, I'd like to build a rack & pinion rail for the gyro to travel on so that it can go up extremely steep inclines without a problem. Hardware list: 3:1 GT2 Belt + Pulley set: https://www.amazon.com/dp/B08QZ4365D 4S 1.3 Amp hour Battery: https://www.amazon.com/1300mAh-Battery-Airplane-Skylark-Nighthawk/dp/B0784CDD6F 2-4S 30A ESC: https://www.amazon.com/dp/B08K4LHQNZ Servo tester: https://www.amazon.com/HiLetgo-Consistency-Controller-Adjustment-Helicopter/dp/B07TQSKLBK The motor i used is out of production, but pretty much any other brushless motor of a similar KV will work fine. Kevin MacLeod - Groove Groove Eric Skiff - Underclocked Kevin MacLeod - George Street Shuffle
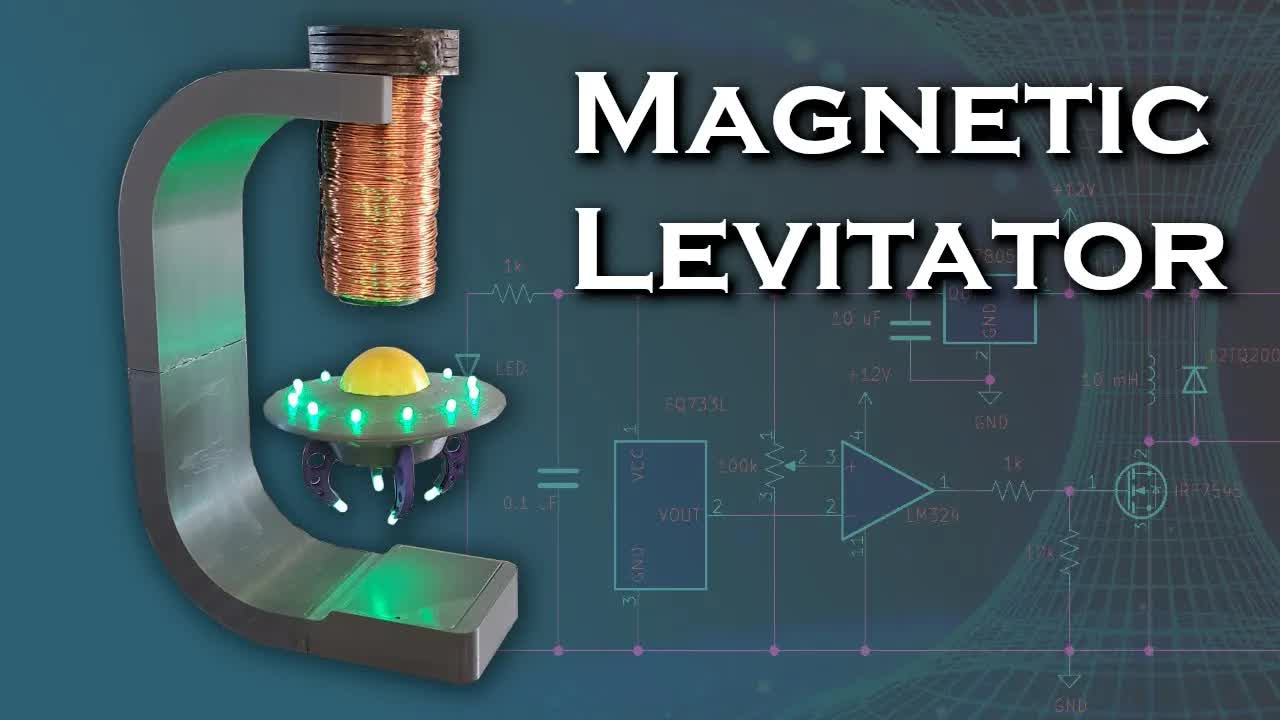
eOT_G-1ogn4 | 28 Dec 2021
Update 7/21/2022: STL files for the levitator have been uploaded https://www.thingiverse.com/thing:5438518 In this video I'm going to show how to build a attractive-type ("hanging") magnetic levitator. This is the easiest type of levitator to build, because the electromagnet only operates with one polarity, and only requires a single sensor and transistor to operate. A repulsion-type levitator requires sensors for X and Y position, and 4 coils with their own individual H-bridge drivers. The electromagnet is built from a 2" x 6" solid steel cylinder as a core, and 600 turns of 16-gauge wire. The longest distance I've managed to attract a large N52 magnet was about 9 inches using 20 amps of current, but the coil heats up very fast with that much current. In this video, the magnets shown are hovering just outside the region where the ferromagnetic attraction to the core would overcome gravity, so the levitator takes very little power. Levitating a 3-lb steel wrench only consumed ~5W, and a 30mm N52 magnet by itself consumes about 1W levitating a distance of about 2" below the electromagnet. The limiting factor in the levitation distance is the resolution of the hall-effect sensor, which has an output of 20 mV/mT. Once a 30mm N52 magnet goes beyond ~2 inches from the sensor, the output is too small to be distinguished against the idle voltage of the sensor. Changing to a more sensitive hall effect sensor would increase the levitation range dramatically, but also consume exponentially more power. There is no microcontroller driving the electromagnet. The coil is energized by a MOSFET that has its gate connected to the output of an LM324 acting as a comparator. One input to the LM324 is the hall effect sensor output, and the other input is a reference voltage set by a potentiometer. I've found that it's neccesary to make slight adjustments to the reference voltage when changing to different magnets / loads on a particular magnet. Some of the key components used in this build: -EQ733L Hall Effect Sensor -LM324 Op-Amp -IRF7545 MOSFET -LM7805 5V linear regulator -6.6 mF / 1 mH input filter Some other figures: -12-18V input voltage -50-500 mA of current draw @ 12V depending on the load -9.5 mH / 1.3 Ohm electromagnet (600 turns of 16 AWG) -Magnets used in this video are 30x5 N52 magnets stacked together and 2x 40x20 N52 magnets stacked together Music used: Serge Pavkin - Fractal Serge Pavkin - Tech Research Serge Pavkin - Intergalactic Alexander Nakarada - Space Ambience

QHonF5h8tqo | 18 Dec 2021
Update (5/19/2023): STL files can be found at the link below: https://www.thingiverse.com/thing:6034389 In this video I'll show how i made a magnetic monorail train that uses infrared LEDs and phototransistors to trigger coils that accelerate it around a track. I built this because i wanted a train to go around my christmas tree and this seemed a lot more interesting than a regular toy train on rails. The infrared tripwire that triggers the electromagnet coils is the same design i used for my second ball accelerator, which is described in detail in this video: https://www.youtube.com/watch?v=uNbL3tRZeMQ The train technically isn't a truly "levitating" train, because it straddles the rail, and its legs prevent the instability of magnetic repulsion from throwing it off to the left or right. A true maglev would have no physical contact with anything below or beside it. I'm working on a true levitating train for a future video, but it was too difficult to implement as a christmas decoartion. IR LED / Phototransistor set: https://www.amazon.com/Gikfun-Infrared-Emitter-Receiver-Arduino/dp/B01HGIQ8NG Music Used: Christmas Village - Aaron Kenny Jolly Old St Nicholas (Instrumental) - E's Jammy Jams Jingle Bells (Instrumental Jazz) - E's Jammy Jams

GJcQfJ6JTZg | 24 Nov 2021
Update 2/24/2022: I've uploaded the STL files for the machine. Note that not all of these parts are used in the final iteration and I didn't sort them yet https://www.thingiverse.com/thing:5261994/files Update 1/17/2022: Schematics and code are linked below. Currently I only have the values for 26 AWG in the code so you'll have to extrapolate for other wire gauges https://drive.google.com/file/d/16xQJ93vJ1Sos_FNN_Kw97RhwrQ_QuLfG/view?usp=sharing https://drive.google.com/file/d/1ZFmob1WSLG9xLbMRCjPKKMHWxX1yLvsC/view?usp=sharing In this video I'll show how i made a machine to automate the process of coil winding. It can be used for electromagnets, tesla coils, loopstick antennas, transformers, generator coils or indcutive chokes - all things I use a lot of. Code, Schematics, STLs: I'm still making a few tweaks. Check back in a few days and I'll update this field with links to all of these. Hardware: -3A / 12V Wall wart with 5.5mm barrel jack -A4988 Stepper Motor Drivers -NEMA17 Stepper Motors -3d printer leadscrew (8mm pitch?) -20mm V-slotted rail -M5 screws + T-nuts for railing -M3 screws for motor mounts / set screws -16x2 LCD with I2C bus driver -LM7805 For logic supply -ATMega328P-PU as the brain Music: Kevin MacLeod - George Street Shuffle Serge Pavkin - Tech Research Serge Pavkin - Futuristic Documentary
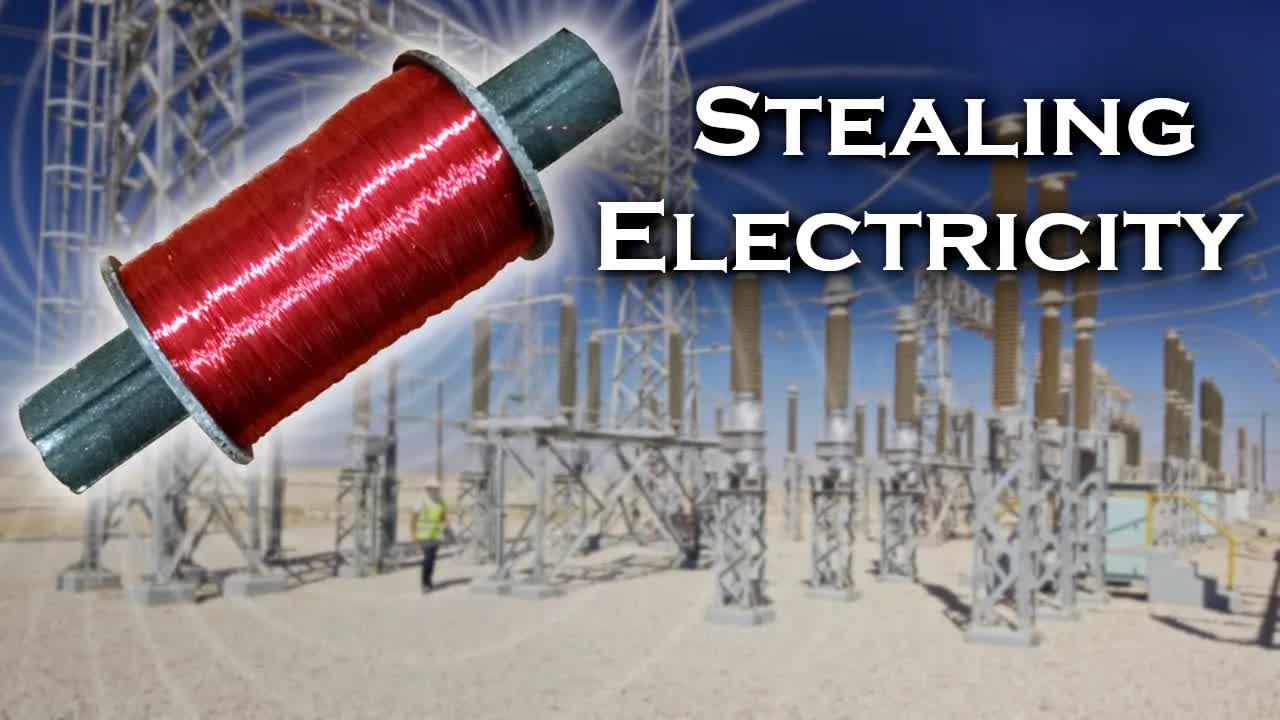
CLS8pbDNHbk | 10 Nov 2021
In this video i build a coil that's effectively a huge loopstick antenna with tuning capacitors to resonate at 60 Hz, which is mains frequency in North America. The coil can generate over 5 volts near running appliances or power cables, and charge a capacitor or light up some LEDs. It works by collecting the small magnetic flux leakage that every AC device produces. The power generated is less than 100 μW in most cases, so it can't do anything very exciting, but it's really interesting to stand under a power line and see a capacitor charge from its leak. The biggest limiting factor seems to be that transmission lines which have opposite phases very close to each other result in a near-zero magnetic field at a distance from canceling out most of each others magnetic flux. Some figures: Coil Wire Gauge: 28 AWG Number of turns: ~12,000 Coil Inductance: 28.1 H Capacitor Value: 250 nF Parts: Coil Core: https://www.amazon.com/CynKen-35x200mm-Ferrite-Loopstick-Antenna/dp/B07PDG87V8 3 lb 28 AWG Magnet Wire: https://www.amazon.com/BNTECHGO-AWG-Magnet-Wire-Transformers/dp/B07H4FQ8RS?th=1 Music: Kevin MacLeod - George Street Shuffle Kevin MacLeod - Groove Groove
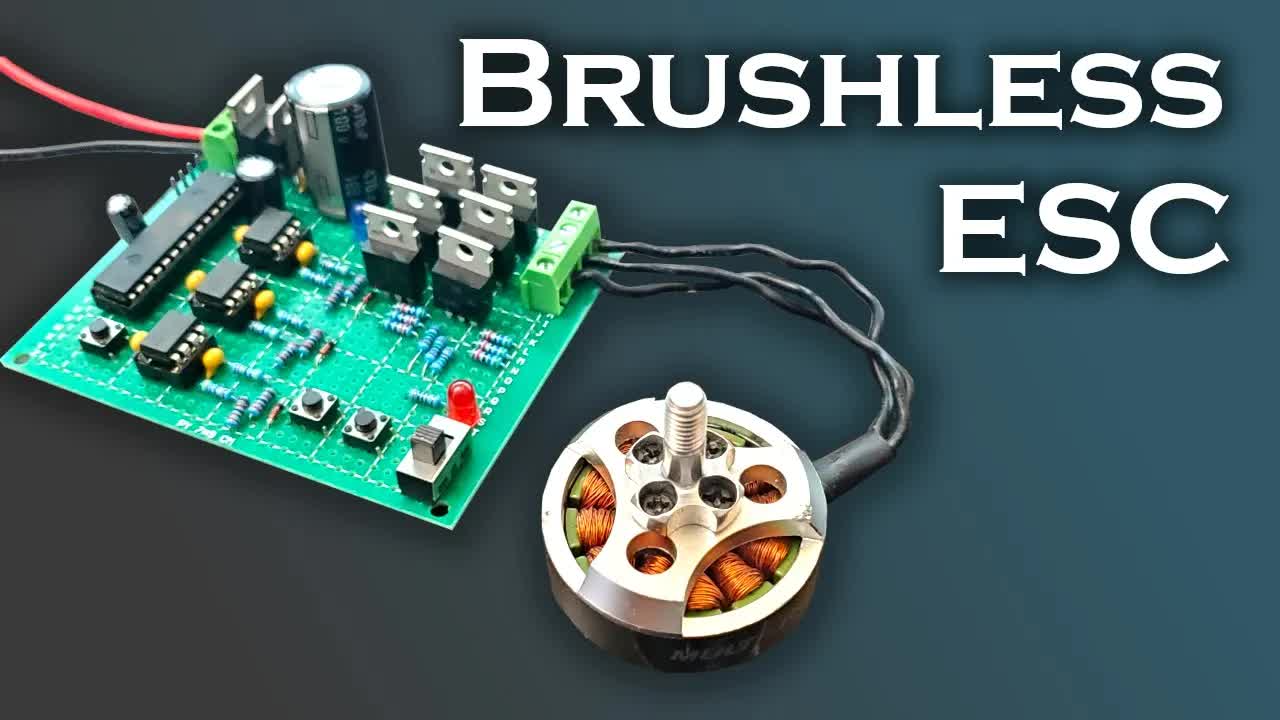
F8l9Z1HGYcU | 02 Nov 2021
In this video I'm going to show how i built a brushless DC (BLDC) ESC (electronic speed controller) based on an Atmega328P microcontroller. This ESC was a prototype for a much larger one that I'll be using to drive the 1500-watt motors on my submarine. The video also explains the theory behind how a brushless DC motor works, and some troubleshooting tips that you may find helpful if you build one of these yourself. The code i used for the first test can be found here: https://simple-circuit.com/arduino-brushless-dc-motor-controller/ I later modified it to add a reverse function and adjusted the startup sequence settings to get a smoother start to my motors. A guide on using the Atmega328P microcontroller by itself (without the arduino board) can be found here: https://www.arduino.cc/en/Tutorial/BuiltInExamples/ArduinoToBreadboard Hardware used: MOSFETs: IRLZ44 Flyback Diodes: MUR120G MOSFET Drivers: IR2101 5V Linear Regulator: LM7805 MOSFET Driver supply regulator: LM317 The motor used in the first part of this video is a very old brushless motor i used to fly on a drone, and I'm not sure what the part number is or if it's still in production. The submarine motors are Turnigy SK3 6374-192 kV brushless motors. I've replaced their ball bearings with bronze sleeves, and coated the rotor and stator with enamel to protect against saltwater. Arduino Code: https://drive.google.com/file/d/1R6ROvEKI6wiVP7WfA2kJ13AO4JUQrIZ_/view?usp=sharing

X31B1pVow1o | 18 Oct 2021
NOTE: The schematics incorrectly show the NPN transistors in reverse, with collector / emitter swapped. This is my first attempt at doing a semi-serious project using digital logic. To really gain a good appreciation for the technology involved, i designed and built the circuit entirely out of discrete transistors instead of using pre-made IC's with logic gates (such as 74-series chips). This adder is built entirely out of 2N3904 NPN transistors, 220k resistors for inputs, and 47k resistors for output pull-ups. There are a total of 152 transistors and 224 resistors, not including the LED resistors on the manual switch board. The first board in the stack uses an LM7805 and 10 uF capacitor to provide voltage regulation. Because of the presence of a carry output bit on the 8th stage, this can technically output a 9 bit number. The A and B inputs are a single byte (8-bit value), so their maximum is 255, and the output can compute up to 510. In the future I'm going to add a lot more features to this machine, like multiple RAM addresses than I can read/write to, a clock + ripple counter to increment the input bits automatically, and maybe even a binary-BCD converter which I could then use as an input to a 7-figure number display, which would give this computer a graphic output. I also want to add a reader for a 3d-printed punch card that will provide program instructions or data. Music: Kevin MacLeod - Groove Groove Heatley Bros. - Dimension Drift Prod Riddiman - Lost Time Kevin MacLeod - George Street Shuffle

1EabqJJnWhc | 09 Oct 2021
In this video I show the differences between an ignition coil (pulse transformer) and other types of transformers, and a few different ways to drive them to get a high voltage output. An ignition coil is an induction coil that has a relatively high primary inductance, but low turns ratio. It generates high voltage by building up a large magnetic field in its primary, and then suddenly collapsing it when current is shut off. The sudden collapse causes a voltage spike in the primary, which is stepped up even further in the secondary coil. These devices can easily produce 30,000 - 40,000 volts with a 12 volt input, and a modest turns ratio of between 15-20. In the video i show how to drive one with a relay, single MOSFET, inductively coupled MOSFET half bridge, and a 600V IGBT, which was by far the most powerful and effective circuit. Some important components: -555 Timer -LM7805 Linear Regulator -IRF640 200V / 18A MOSFET -12TQ200 200V / 15A Diode -MUR120G 200V / 1A Diode -STGP20H60DF 600V / 20A IGBT (Best results by far) -1N4148 Diodes for duty cycle adjustment Ignition coil used: https://www.amazon.com/gp/product/B00809W952/ref=ppx_yo_dt_b_search_asin_title?ie=UTF8&psc=1 Music: Serge Pavkin - Modern Technology Kevin MacLeod - George Street Shuffle Heatley Bros. - Otherworld Serge Pavkin - Intergalactic

USiW2xFOSFg | 21 Sep 2021
This is my first attempt at building a high voltage impulse generator, better known as a "Marx" generator, after its inventor, Erwin Marx. This is similar to a capacitor-diode voltage multiplier, but produces the voltage multiplication in brief pulses rather than continuously. The circuit has 16 stages, each consisting of a 1 nF 20,000V capacitor, with 880k resistors on both the high and low side. Each 880k resistor actually consists of 4 220k resistors in series. This was done to divide the voltage across the resistors to prevent high voltage from jumping over the resistor from one lead to the other. The High Voltage DC source for the input to the generator is the same as i used in my voltage multiplier video, which provides more detail on the design: https://www.youtube.com/watch?v=SmjKbNoK6nU&t=9s The biggest arcs i managed to produce were 9.5" (24 cm) long at 320,000 volts. In theory, 320,000 volts should only cross ~4" (10~11 cm), because the breakdown voltage of air at 1 atmosphere is ~3MV/m. However, because of the sharp point on the positive electrode, a concentration of electrical charge forms which increases the effective voltage across the terminals. Because of that, actual breakdown voltage ends up being 1~2 MV/m depending on electrode geometry The arcs are long, but not particularly powerful. At 20KV, each 1nF capacitor only stores 0.2 Joules of energy, so an arc at full charge would contain no more than 3.2 Joules of energy. Parts of interest: 20 KV / 1 nF caps: https://www.amazon.com/Voltage-Ceramic-Capacitor-0-001uF-1000pF/dp/B07K6PH4SR/ref=sr_1_3?dchild=1&keywords=20kv+capacitor&qid=1632244619&sr=8-3 20 KV / 100 mA Diodes: https://www.amazon.com/2CL2FM-100mA-Voltage-Diode-Rectifier/dp/B074S8JT96/ref=sr_1_6?dchild=1&keywords=20kv+diode&qid=1632244647&sr=8-6 Flyback Transformer Core(s): https://www.amazon.com/5pairs-UY1658-Transformer-ferrite-Material/dp/B0146OG8VK/ref=sr_1_3?dchild=1&keywords=flyback+transformer+core&qid=1632244665&sr=8-3 Music: Serge Pavkin - Digital Future Serve Pavkin - Fundamental Analysis Serge Pavkin - Modern Technology

iXu-ForqR-M | 18 Sep 2021
In this video I'm going to show how interrupter modulation can change the shape / size of the tesla coil's arc and use an arduino to play music with square wave tones. The circuit is the same as in part 3, except I've reduced the number of turns on the primary coil from 4 to 2, and I'm providing a 30V input instead of 120V after having a few fireballs resulting from the mis-use of 120VAC. In the musical portion of the video, i 3d print a keyboard that plays major notes from C2 to C3, and can trigger different musical routines from specific button combinations. The songs are hand-written based on notes i played by ear with a browser-based tone generator, because I haven't figured out how to play MIDI files with the arduino yet. The tone generator can be found here: https://www.szynalski.com/tone-generator/ The previous parts of this video can be found here: Part 1: https://www.youtube.com/watch?v=CdUaW9StZwg&t=9s Part 2: https://www.youtube.com/watch?v=U_dhVrOCprA Part 3: https://www.youtube.com/watch?v=ncHoBamK9jA&t=818s

T66Ig4iOcig | 02 Sep 2021
This is a rebuild of an RC lawnmower i built several years ago, but using an electric mower this time. It pretty much operates the same way an RC car / battlebot type vehicle does with just two opposable motors and casters for front wheels. In the future I plan to outfit the mower with FPV so that i can drive it from inside the house, and possibly do automation even further down the road. Here's a list of my hardware: - (2x) 35 A-h 12V lead acid batteries - 275-Amp battery disconnect switch https://www.amazon.com/gp/product/B07T288VN8/ref=ppx_yo_dt_b_asin_title_o01_s00?ie=UTF8&psc=1 - Turnigy 9x 2.4 GHz transmitter / reciever (100 mW tx power, i think) - Sabertooth 2x32 dual brushed ESC (32 Amp / 33.6V max.) https://www.dimensionengineering.com/products/sabertooth2x32 - 1" x 1" x 1/16" thick square tubing, welded with 0.030" flux cored wire - (2x) 80mm 12V fans Music: Kevin MacLeod - George Street Shuffle Heatley Bros. - Dimension Drift Heatley Bros. - Sunset Beach

ncHoBamK9jA | 18 Aug 2021
This is part 3 of my video series on designing and building a Solid State Tesla Coil (SSTC). Part 1: https://www.youtube.com/watch?v=CdUaW9StZwg&t=342s Part 2: https://www.youtube.com/watch?v=U_dhVrOCprA In this video I'll show the following: -How to build a full H-bridge driver -How to use secondary coil current as feedback to drive the primary coil -How to adjust the phase of the driver to maximize output power -Results of running the coil off mains (120VAC) instead of 30V DC Hardware used is mostly the same as part II, with a few differences: -IXTQ36N30P 300V / 36A MOSFETs for the H-bridge -2200 uF 400V Filter Capacitor for mains voltage -BOTH sides of the gate drive transformer primary have DC blocking capacitors. Having DC blocking on only one side caused some weird level shifting problems that resulted in erratic output. -300A/1600V Bridge Rectifier (massive overkill, but i happened to have it already) https://www.amazon.com/gp/product/B075L3QGH1/ref=ppx_yo_dt_b_search_asin_image?ie=UTF8&psc=1 Music Used Serge Pavkin - Modern Technology Serge Pavkin - Heavy Industry Serge Pavkin - Fundamental Analysis Serge Pavkin - Digital Future Serge Pavkin - Innovative technology

U_dhVrOCprA | 23 Jul 2021
This is Part 2 of my video series on designing and building a Solid State Tesla Coil (SSTC). Link to Part 1: https://www.youtube.com/watch?v=CdUaW9StZwg&t=342s In this video, I'm going to show the following: -Finding the resonant frequency of a Tesla Coil with a Signal Generator and Oscilloscope -Problems with single-MOSFET designs, and why they should be avoided -How to design/build a half-bridge inverter to drive the primary coil -Signal conditioning with inverted schmitt triggers and RC delay circuits to change phase / duty cycle -Using dedicated MOSFET gate drivers and coupling their output with a signal transformer to isolate the driver logic from the half bridge -Design of an interrupter to modulate the output of the coil Hardware used: -2"x12" PVC secondary former with 1,200 turns of 30 gauge wire -4-turn, 3.5" diameter primary coil -Approximately 6"x6" aluminum plate as a ground plane -TLC555 (High speed timer for up to 2.1 mHz) -NE555 (Low speed timer for interrupter - 100 kHz max) -CD74HC14E Hex Schmitt Trigger inverter for signal conditioning -TC4422 MOSFET Driver chips (9A max / 18V vcc max) -IRF540 (100V max) MOSFETs for half-bridge -MUR120G diodes for half-bridge -30mm toroid wound with 25-turn trifilar winding of 26 gauge wire for the gate drive transformer In the third video, I'm going to cover how to use secondary coil feedback to drive the primary coil, signal phase shift, and the construction of a full-bridge inverter powered with mains voltage (120V). Music used: Serge Pavkin - Innovative Technology Serge Pavkin - Tech Research (full version) Serge Pavkin - Tech Serge Pavkin - Positive Things Serge Pavkin - Unknown Serge Pavkin - Business Infographics Serge Pavkin - Intergalactic

CdUaW9StZwg | 11 Jul 2021
This is the first part in series where I'm going to try to build a solid state tesla coil (SSTC) without any prior experience in doing so. In this video i start off driving a tesla coil with a ZVS oscillator circuit connected to the primary, which doesn't work very well because there's no ability to adjust the frequency (aside from sliding a contact along the primary coil) and driving at resonance is unstable because the ZVS circuit will want to "drift off" when it sees the huge load that occurs at resonance. The second, somewhat more successful circuit used a 555 timer to drive a single MOSFET on/off to oscillate the primary at resonance. This allowed me to dial in the resonant frequency with trimmer knobs, but it was easy to overshoot it, and i killed several MOSFETs in the process. The FET I'm using for all these videos is an IRF250, and the videos shown are mostly with 12V of input, although in some of the clips there's 30V in. I use a PNP-NPN pair as a push-pull driver for the gate, but since these aren't moving more than about 200 mA, i think the gate isn't being driven hard enough, which is causing huge switching losses. In the next video, I'm going to cover the proper procedure for tuning a tesla coil with an oscilloscope, driving the primary coil using feedback signals from the secondary coil, and techniques to avoid obliterating my MOSFETs. Music Used: Heatley Bros. - 8 Bit Go Serge Pavkin - Fractal Serge Pavkin - Tech

v7t6dXT-Ffs | 19 Jun 2021
In this video I build a 12" 3d printed waterwheel and use it to generate electricity from a tiny amount of water flow. The parts are all printed from PLA. It uses a 10x gear ratio to drive a rotor with 99 neodymium fridge magnets on it and generate alternating current through 33 coils. I measured the maximum power output of a the generator at about 26 mW, and the whole thing is only ~9% efficient, so there's definitely room for improvement. I think I can achieve a larger gear-up ratio without adding much friction, which could dramatically increase the power output. The shafts / bearings are 8mm, and i used 8mm x 3mm neodymium magnets for the generator rotor. The LED sets are wired antiparallel so they illuminate on opposite phases of the generator's AC output. Since I live in a very flat place with no natural streams nearby, I got the water flow from a tiny aquarium pump which only moves a few LPM. The wheel runs at about 35 RPM in the sink and about 20 RPM on the pump. STL Files: https://www.thingiverse.com/thing:4889445 Music used in the video: Kevin MacLeod - George Street Shuffle Kevin MacLeod - Groove Groove

mcD3uBld4Y4 | 05 Jun 2021
This video shows how to build a radio that transmits a simple 1 kHz tone on the AM band, which can be heard in a handheld radio or car radio up to 100 yards away. The radio uses an LC oscillator to drive a push-pull amplifier made from a 2N3906 and 2N3904 transistor. The audio tone is generated by a 555 timer. The radio can be powered by up to 40V, but in this video I'm only using 12V. I experimented with transmitting on 1030 kHz then increased my frequency to 1620 kHz by changing the capacitors in the LC oscillator that generates the carrier wave. Because the frequency is so low in both cases, the antenna is nowhere near the wavelength, or even quarter wavelength. For antennas shorter than L/4, two major problems occur: -The radiation resistance is extremely small (i.e. only a very small amount of the current in the antenna actually travels out as radio waves) -The antenna acts as a capacitor and has huge impedance from capacitave reactance. In the video, i attempt to balance out the capacitave reactance with an adjustable inductor (or "loading coil"), with fairly good results. The total power radiated was well below 1 mW in both cases. This is probably less power than something like a garage door opener transmits. Note that radio transmissions in the US/Canada/Europe are regulated, and this device is only for demonstration. If you want to build a larger power transmitter, make sure you've got an amateur license and use one of the frequency bands allocated to amateurs. Serge Pavkin - Business Infographics Serge Pavkin - Commercial Agreement Serge Pavkin - Fundamental Analysis Heatley Bros. - Dimension Drift Kevin MacLeod - George Street Shuffle

cRY7HEzoOwk | 23 May 2021
This video shows how I built a mechanical inverter/transformer, which can take 3V DC from a pair of AA Batteries and turn it into 700V. A long time ago before I knew how to build a solid state inverter circuit, I was curious about building a device like this as an alternative to generate AC from DC. It isn't really practical, but it's a really interesting toy to build/play with. I use 16 6mm x 4mm neodymium magnets for the rotor with alternating N-S-N-S polarity and 16 coils made from #6 screws wound with about 1,300 turns of 32 gauge magnet wire. The rotor is driven by a 3V motor that turns at about 2,800 RPM. The multiplier circuit uses 100 nF film capacitors with 1N4006 diodes. Music: Heatley Bros - Otherworld https://www.youtube.com/watch?v=1GYItux32P4 Heatley Bros - 8 bit chillout https://www.youtube.com/watch?v=8El8ZP8LMFE
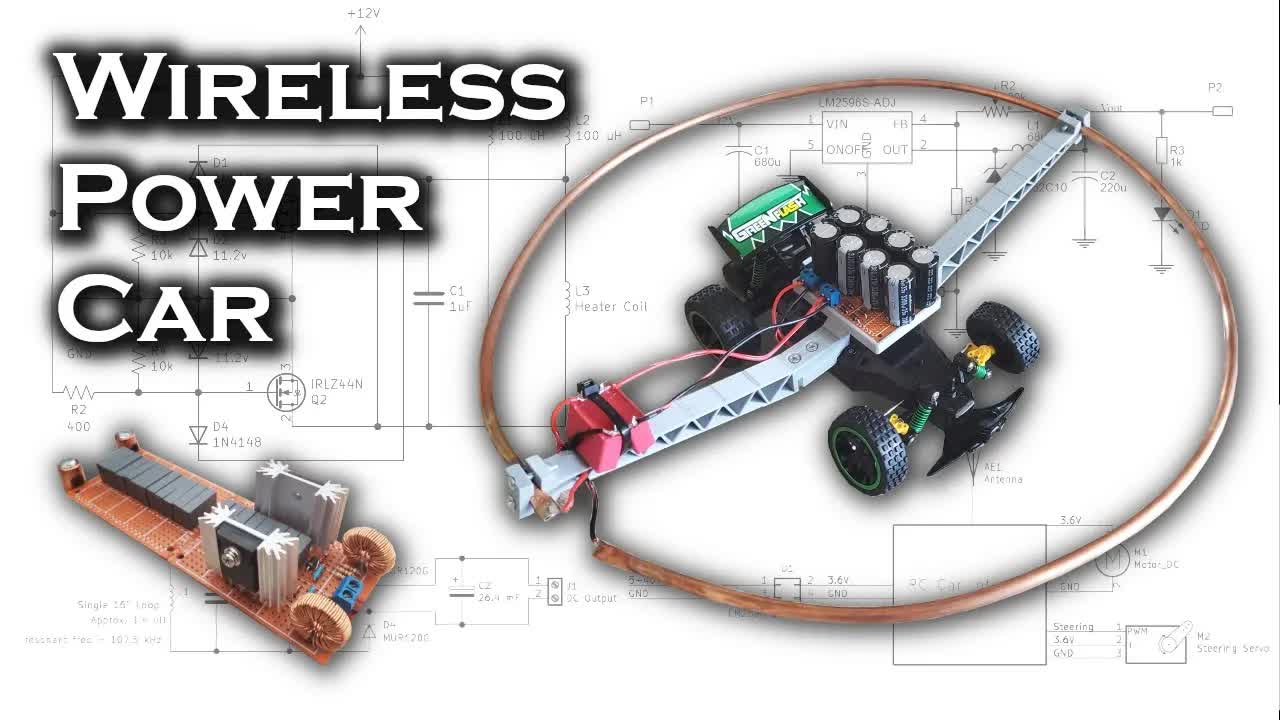
on3sQQa88dE | 16 May 2021
This is an upgraded version of the wireless power transmitter from my previous video being used to power a small 3.6-volt RC car. The transmitter/receiver resonate at 100 kHz, and a bridge rectifier on the RC car feeds a DC-DC buck converter that steps the voltage down to 3.6V. The car pulls around 1 amp, so the transmitter has no problem powering it as long as it's inside the loop or within about 1 ft outside the edge. The transmitter runs at 31V and consumes 3-4 amps depending on the load. Harware used: RC Car: https://www.amazon.com/dp/B07X7MRG3F?psc=1&ref=ppx_yo2_dt_b_product_details DC-DC Buck Converter (3.0-40V in / 1.5-35V out): https://www.amazon.com/dp/B06XZ1DKF2?psc=1&ref=ppx_yo2_dt_b_product_details Transmitter / ZVS Driver: -2x IRF250 Mosfets -2x MUR120G Diodes -2x 13V Zener Diodes -2x 120 uH 5A inductors -20x 47 nF 400VAC capacitors rated at 14 mOhm ESR -2x Copper lugs from Home Depot -1/4" Copper tubing Receiver / Rectifier: -2x 1uF 600V Capacitor -1/4" Copper tubing (~16" diameter) -8x 35V 3300 uF Capacitors -4x MUR120G Diodes 3d printed parts are made from ordinary PLA and modeled in CATIA Induction heater video (explains ZVS driver schematic / how to build): https://www.youtube.com/watch?v=G9mudqJ46xM&t=44s Music Used: Heatley Bros. - 8 bit chillout https://www.youtube.com/watch?v=8El8ZP8LMFE Heatley Bros. - 8 bit emperor's club https://www.youtube.com/watch?v=jy-ZMc2csbE

D9IGjKJaO6w | 02 May 2021
Here i'm going to show how i built a wireless power transmitter / receiver that can power things up to ~2 ft away. The Tx/Rx "coils" are actually single 15" loops of 1/4" copper tubing. The transmitter and receiver are in resonance (just like a Tesla coil), so the maximum amount of power can be transferred. I'm only putting about 40-45 watts of power into my transmitter, so I was very surprised by the results i got. Technical Specs: Loop Inductance: 1.05 uH Resonant Cap value: 3 uF Resonant Frequency: 89.7 kHz MOSFET: IRF640 (200V VDS, 1.5V VGS threshold). This FET has a very high R_DS of about 0.2 ohm so they get very warm and they also go into latch-up easily because of the low gate threshold voltage. I don't reccommend this part, and in future builds I'll be replacing this with an IRF250 or IRF260. Gate Diodes (Also used on rx rectifier): MUR120 (200V / 75 nS recovery time) LED Board resistors: 330 ohm Magnet in the electromagnet part of the video is a 40mm x 20mm N52 In the future I plan to make a dramatically larger ZVS driver that can handle around 1,000 watts and power a 4-6 ft transmitter coil to fly a small drone several feet off the ground, which will be carrying a reciever coil instead of a battery. This type of device is also really useful for transferring power through a barrier, or to a rotating object. Music used: Serge Pavkin - Fractal Serge Pavkin - Tech Serge Pavkin - Network https://www.youtube.com/c/SergePavkinMusic

GUOHjON9RVg | 18 Apr 2021
This is a video about my homemade submarine, which I've been working on off and on for the last 2 years. I'm planning to make some videos with it in the coming weeks, so I thought it would be a good idea to do an introductory video about how i designed/built it. It's a "semi-wet ambient" type submarine, meaning the pressure inside is the same as the outside water pressure, and the cabin is partially flooded. The pilot and passenger sit in a bubble of trapped air underwater that's equivalent to pushing a cup upside down in your sink, similar to a diving bell. Power for propulsion, pumps, and lights is provided by a pair of 12V / 100AH lead acid batteries, which are sealed off against water entry, and have their terminals potted in rubber to prevent corrosion (in future videos, the batteries will be series-connected for 24V). Pneumatics for cabin air and buoyancy control come from a pair of 120 Cubic ft steel air tanks pressurized to 4,000 psi. I have an adapter that allows me to connect regular hardware store NPT fittings to the diving regulators on the tanks. Motors are 12V/30A saltwater trolling motors made by newport that allow me to cruise at about ~3 knots surfaced and about 2 knots submerged. In future videos, I'll be running Turnigy 6374 brushless outrunners specially modified for underwater use with 7.25x5 3 bladed props. My hope is to eventually use this sub to explore reefs and shipwrecks along the Florida coast. Music: Serge Pavkin - Intergalactic Serge Pavkin - Fractal Heatley Bros. - Dimension Drift Serge Pavkin - Universe

SmjKbNoK6nU | 12 Apr 2021
This video shows how to build a cockroft-walton type voltage multiplier using a flyback transformer as a first stage driven by a ZVS driver with a 12V input. This circuit outputs 120,000 volts DC and arcs from ~4" away. Within about 2 feet of the device, you can feel the ion wind, and your hair being pulled toward it by electrostatic induction. I didn't use any current limiting resistors, so the discharges are very dramatic but also extremely hard on the capacitors in the multiplier. After about 4-5 seconds of continuous discharge, there's little to no output, and the device needs a minute or two to recover before it can be used again. My guess being that the caps are swelling under such a high load. The flyback and ZVS driver are both homemade. The circuit for the ZVS driver is explained in more detail in my video on induction heating : https://www.youtube.com/watch?v=G9mudqJ46xM&t=2s Parts List: -1nF / 20kV Capacitors: https://www.amazon.com/gp/product/B07V3XMHHL/ref=ppx_yo_dt_b_asin_image_o01_s00?ie=UTF8&psc=1 -20 kV / 100 mA Diodes: https://www.amazon.com/gp/product/B07MVX689B/ref=ppx_yo_dt_b_asin_image_o05_s00?ie=UTF8&psc=1 -Ferrite U-cores for flybacks: https://www.amazon.com/gp/product/B0146OG8VK/ref=ppx_yo_dt_b_search_asin_image?ie=UTF8&psc=1 -32 AWG magnet wire for secondary windings -IRLZ44 MOSFETs with heatsinks for ZVS driver -1N4148 Diodes for gate pull-downs Music: Serge Pavkin - Fractal Serge Pavkin - Network Serge Pavkin - Unknown
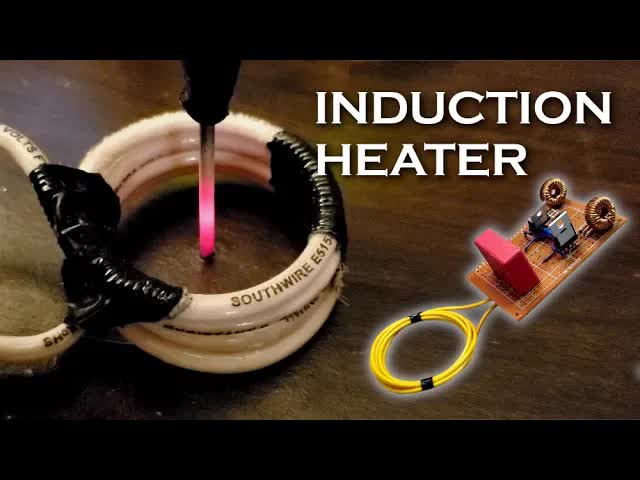
G9mudqJ46xM | 04 Apr 2021
This video shows how I build a ZVS driver to power a small induction heater than can make pieces of metal weighing ~1 gram or less glow red hot. The circuit takes in 10-16V and the final variant shown in this video oscillates at about 160 kHz. I also show how this circuit can be used to drive a flyback transformer. This is a very modestly powered circuit, but the advantage of a ZVS driver is that it can be scaled up to tens of kW without much of a problem. The voltage on the coil (and the MOSFET V-DS) is about 3 times the input voltage, so to use higher voltages of say, 36 or 48V, I would need MOSFETs rated for a higher V-DS like an IRF250 or IRF460. NOTE: My statement about inductance not changing is inaccurate. Inserting a ferromagnetic object into the coil *does- increase the inductance and reduce the frequency. Hardware used: IRF44 Mosfet 1N4148 Diode 5.6V Zener Diodes 400 Ohm Gate Resistor 10k Gate pulldown resistor 1 uF 630V Polypropylene film capacitor Music: Kevin MacLeod - George Street Shuffle Serge Pavkin - Fractal

KefetoLcZgE | 14 Mar 2021
This video shows how to make a plasma tube out of a glass bottle and a high voltage supply that takes advantage of Paschen's law (https://en.wikipedia.org/wiki/Paschen%27s_law) to generate a long electrical arc from the reduced breakdown voltage of air in a low-pressure environment. The bottle runs at about 0.1 atmospheres, so this would be considered a very low vacuum, but it's more than sufficient to demonstrate the relationship between breakdown voltage and pressure. A dedicated vacuum pump could evacuate this bottle down to a few thousandths of an atmosphere, and the same size arc could be generated with a few hundred volts instead of 30,000 volts. -Diamond hole bits used in the video: https://www.amazon.com/gp/product/B01L92YM1A/ref=ppx_yo_dt_b_search_asin_image?ie=UTF8&psc=1 Music: Serge Pavkin - Technology For Life https://www.youtube.com/watch?v=caIqdAb5w7o&list=PLGR5IhV9jJZHLLkv-EeVNCKogv8Hb9L6O&index=90 Serge Pavkin - Intergalactic https://www.youtube.com/watch?v=0Z0vPtMEvVg&list=PLGR5IhV9jJZHLLkv-EeVNCKogv8Hb9L6O&index=142

npypgEVxdRU | 07 Mar 2021
This is a simple bipolar Tesla coil that's small enough to touch while it's running. A bipolar tesla coil is simply a tesla coil that has both sides of its secondary coil connected to electrodes facing each other, as opposed to a typical tesla coil which uses earth ground (or a sufficiently large ground plane) as one pole of its secondary coil. This is probably the cheapest, easiest, and most convenient way to create a very high voltage power supply - simply a dimmer switch and an ignition coil. The output of my supply is over 30,000V DC. Here's a list of the hardware i used: Box - Hobby Lobby 6uF/220V Capacitor - Salvaged from an old microwave. This part is equivalent to the one i had: https://www.amazon.com/CAPACITOR-250VAC-APPLI-PARTS-6-250/dp/B01FY4CYQY/ref=sr_1_1?dchild=1&keywords=6+uF+cap&qid=1615147679&sr=8-1 600W Dimmer Switch - https://www.amazon.com/gp/product/B000FK9WYU/ref=ppx_yo_dt_b_search_asin_title?ie=UTF8&psc=1 Ignition Coil - https://www.amazon.com/gp/product/B00809W952/ref=ppx_yo_dt_b_search_asin_image?ie=UTF8&psc=1 Primary Wire: 12 turns of 12 AWG Solid copper Secondary Wire: ~1700 turns 32 AWG magnet wire Electrode Arms: 1/4" Copper Tubing Electrode Tips: https://www.amazon.com/gp/product/B07RBL5TQS/ref=ppx_yo_dt_b_search_asin_title?ie=UTF8&psc=1 Everything else is 3d printed with PLA on a Prusa MK3S. Music List: Serge Pavkin - Network https://www.youtube.com/watch?v=Y35itcKMznM&list=PLGR5IhV9jJZEdLL9SeM9OmuwK0ve3RxR7&index=10 Serge Pavkin - Unknown https://www.youtube.com/watch?v=NL1C6Kc0yic

UUI0k7w_09g | 05 Mar 2021
In this video I'm going to use a pulse of current from a 1,200 volt capacitor bank to launch metal objects through electromagnetic induction. This is a really interesting area of electromagnetism, because it's effectively generating a huge repulsive magnetic force between two objects without any magnets actually being involved. The large electromagnet used in the second part of the video is from a microwave transformer. The core can be sliced fairly easily with an angle grinder if you make your cuts right at the weld lines. As a transformer, magnetic flux is circulated between the primary and secondary windings, but with one end open, magnetic flux is free to "leak" out into space, turning the transformer into an electromagnet. This is probably the cheapest and easiest way to make a very powerful electromagnet. Hardware List: Power Source - 12V / 450 mAh LiPo battery Rectifier Diodes: 4kV 0.25A - GP02-40-E3/54 (x4) Capacitors: 2200 uF 400V - E36D401CJN222MC92M (x3) Transformer Secondary Wire gauge - 28 AWG Launch coil wire gauge - 18 AWG https://www.amazon.com/gp/product/B0714GN73V/ref=ppx_yo_dt_b_search_asin_image?ie=UTF8&psc=1 ZVS Driver + Flyback Transformer package: https://www.amazon.com/Driver-Flyback-Generator-Jacobladder-Ignition/dp/B08GZBLFMG/ref=sr_1_4?dchild=1&keywords=zvs+driver&qid=1614903803&sr=8-4 (I didn't use the included flyback primary/secondary but wound my own instead) Music: Serge Pavkin - Fractal https://www.youtube.com/watch?v=8CFs1bVmCAg Serge Pavkin - Network Serge Pavkin - Tech https://www.youtube.com/watch?v=8CFs1bVmCAg

Wedh-vp-pWI | 16 Feb 2021
In this video i make a tiny electromagnetic mortar powered from a 110V outlet. The coil consists of 150 turns of 24-gauge wire encapsulated in ferrous material to increase efficiency. The capacitor bank is 1.45 mF @ 155V, carrying a total of 17.4 J of energy in the form of static electricity. An 8.1 gram steel ball reaches a maximum height of 12 ft, so i estimate an efficiency of 1.7%. Music: Prod. Riddiman - Lost Time https://www.youtube.com/watch?v=5xUVDz5ha5U Heatley Bros - Luminaire https://www.youtube.com/watch?v=-c0EVoYGJRY

uNbL3tRZeMQ | 13 Feb 2021
Update 9/5/2021 - STL Files in link below: https://drive.google.com/file/d/150P90fzySc2uXoxUL0e2ZlGPpEaGcZzJ/view?usp=sharing In this video I make a new version of my ring accelerator that's capable of propelling steel balls 15 times faster than my first design. This is the second part in a series about improving accelerator coils Here's some technical specs: Input voltage: 24V Number of coils: 4 Wire Gauge: 24AWG Coil Current: 13A Coil ID: 1.1" Coil OD: 1.4" Coil Length: 0.5" Coil turns: 200 The final outer diameter is ~2" due to the addition of steel wire to create a magnetic flux guide or "shell". FET Type: IRLZ44N On time: ~8 ms at max. speed Energy input per pulse: 2.6J Ball mass: 65 grams Ball kinetic energy: ~0.52J Part I: https://www.youtube.com/watch?v=OIw1JiMGHlw Previous Accelerator design: https://www.youtube.com/watch?v=qfmv-rHK_RU&t=2s Music: Serge Pavkin - Fractal https://www.youtube.com/watch?v=8CFs1bVmCAg Serge Pavkin - Tech https://www.youtube.com/watch?v=cNnYlaF183I Serge Pavkin - Unknown

OIw1JiMGHlw | 12 Feb 2021
In this video I experiment with different improvements to electromagnet coils and build a test fixture to measure my results and compare them to magnetic finite element simulations. Ultimately, i measured an efficiency increase of 51% on a coil that was covered in a shell of ferrous material acting as a magnetic flux guide. The magnetic simulation software i use is called FEMM 4.2 and it's free to download: https://www.femm.info/wiki/HomePage Part II: https://www.youtube.com/watch?v=uNbL3tRZeMQ Music: Heatley Bros. - Ocean Palance Serge Pavkin - Fractal Serge Pavkin - Tech

2j90m6k2vCo | 29 Jan 2021
The vastly-improved second version of my tiny 2-volt hand cranked generator (https://www.youtube.com/watch?v=0PiGNDu3Oqs). This generator puts out up to 32 volts open-circuit and ~500 mW at optimum load, and can charge a phone/tablet. It's built from a pair of 60mm speaker magnets for the rotor and four 5,000-turn coils of 32 gauge wire. To get the fast rotation of the magnets, i use a 1:10 gear ratio. Music: Unknown - SergePavkinMusic Music Link: https://youtu.be/NL1C6Kc0yic Music: Steady Growth - SergePavkinMusic Music Link: https://youtu.be/Mwcs4CwfybE

qfmv-rHK_RU | 17 Jan 2021
In this video i show how to use an electromagnet with an optical sensor to continuously accelerate ferromagnetic / magnetic spheres around a circular track. A 12V LiPo battery supplies power to a driver board that energizes a 300-turn coil when a sphere approaches, causing it to accelerate into the center of the coil. I've successfully run the device with up to 3 spheres at a time. The electromagnet is far more powerful against a magnetic sphere, but much more erratic and unpredictable, and the sphere tends to stop suddenly after a few rotations. STL files: https://www.thingiverse.com/thing:4918703 Music: Kevin MacLeod - George Street Shuffle Heatley Bros - Dimension Drift
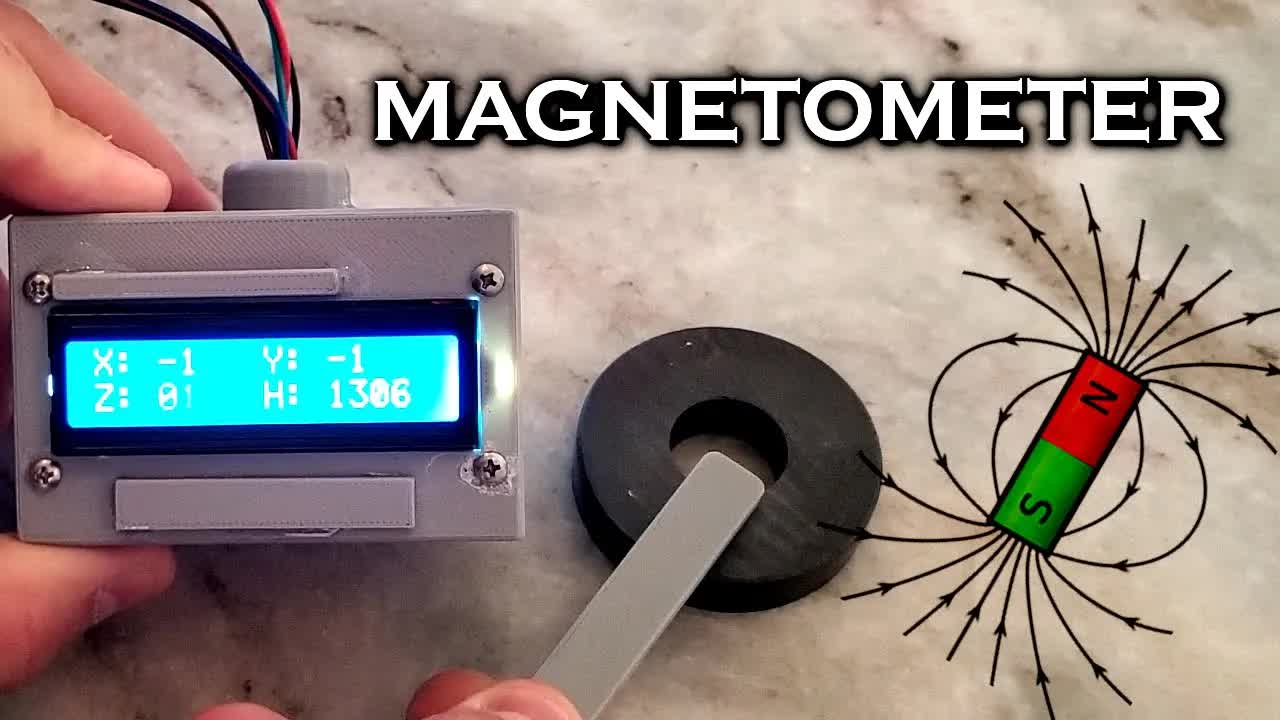
Nm9DAqkCOKU | 15 Jan 2021
This video shows how to create a magnetometer using hall effect sensors. It uses (3) A1309 sensors to read up to +/- 220 Gauss on 3 axes, and (1) A1308 sensor to read up to 1500 Gauss. One Gauss is 1/10,000 Tesla - which is the SI unit for magnetic field strength. NOTE: The part numbers shown in the schematic are reversed. A1309/A1308 are swapped. Parts used: -Atmega328P -A1308KUA-1T -A309KUA-9T -LM317 Guide on burning bootloader / programming an Atmega328: https://www.arduino.cc/en/Tutorial/BuiltInExamples/ArduinoToBreadboard If you're buying brand new Atmega chips, you'll need to burn the bootloader before you can program them, but if you're just pulling the chip off an Arduino, you can skip that step. Music: Heatley Bros - 8 Bit Chillout Heatley Bros - 8 Bit Emperors Club

HY-rKw4qngk | 28 Dec 2020
How to build a 6,000V / 2.4 kW power supply from three microwave transformers. Hardware: -Used microwaves found on facebook marketplace / dumpster -1/4" copper tubing -12 AWG Solid copper wire Music: Kevin MacLeod - Scheming Weasel Kevin MacLeod - RetroFuture

6zdD5Rkx8OE | 26 Dec 2020
Creating a machine to wind Tesla coil secondary coils using 3d printed brackets and a 12V DC gear motor Parts: 100 RPM Gear motor: https://www.amazon.com/gp/product/B0721T1PXQ/ref=ppx_yo_dt_b_asin_image_o06_s00?ie=UTF8&psc=1 5000 mAh 3S Lipo: https://hobbyking.com/en_us/zippy-flightmax-5000mah-3s1p-20c.html Hardware: -Prusa MK3S using PLA -M3 and #6 Screws Soundtrack: Kevin MacLeod - Groove Groove